Ultra-fine grinding of kaolin
The main mineral composition of kaolin is 90% kaolin + 10% halloysite, quartz, jellyfish stone, etc., commonly known as “china clay”. The world’s kaolin resources are rich and widely distributed. At present, the world has identified about 20.9 billion tons of kaolin resources. In the world, the Americas are the main producing areas of kaolin, and kaolin production accounts for about 35% of the world’s total output; Europe’s kaolin production has long been ranked second in the world, accounting for about 30% of the world’s total output.
Kaolin is divided into hard kaolin, light kaolin and sandy kaolin.
Hard kaolin: hard (Mohs hardness 3~4), no plasticity, plasticity only after crushing and fine grinding. This kind of kaolin is dark gray, brown, etc. due to its high-quality impurities.
Lightweight kaolin: soft, generally strong plasticity, sand content <50%.
Sandy kaolin: soft, general plasticity, strong plasticity after sand removal, sand content ≥50%.
Kaolin is widely used and can be used in ceramic industry, paper industry, rubber industry, enamel industry, refractory material industry, environmental protection and chemical industry, etc.
Ceramic industry: mainly used for daily-use ceramics, architectural ceramics, sanitary ceramics, special ceramics and arts and crafts ceramics.
Paper industry: used as fillers and coatings for papermaking.
Rubber industry: used as a filling and reinforcing agent for rubber products.
Enamel industry: Kaolin with high whiteness, fine particle size and good suspension performance is used as silicate glass coating for enamel products.
Refractory industry: multi-clinker refractories, semi-acid refractories, etc.
Environmental protection and chemical industry: production of polyaluminum, treatment of industrial domestic water, production of alum, aluminum chloride and other chemical agents.
The whiteness of kaolin is one of the important indicators that determine its application value. The dyeing impurities in kaolin are mainly iron, titanium minerals and organic matter. Iron and titanium mostly exist in the form of hematite, goethite, pyrite, siderite and other minerals, and their distribution in kaolin is also very complicated, and most of the crystalline ones are mixed with fine particles. Since iron-containing minerals will become Fe2O3 when calcined at high temperatures, the raw materials will turn yellow or brick red. Therefore, measures to remove iron must be taken before or during calcination to increase the whiteness of the product to 92% or higher.
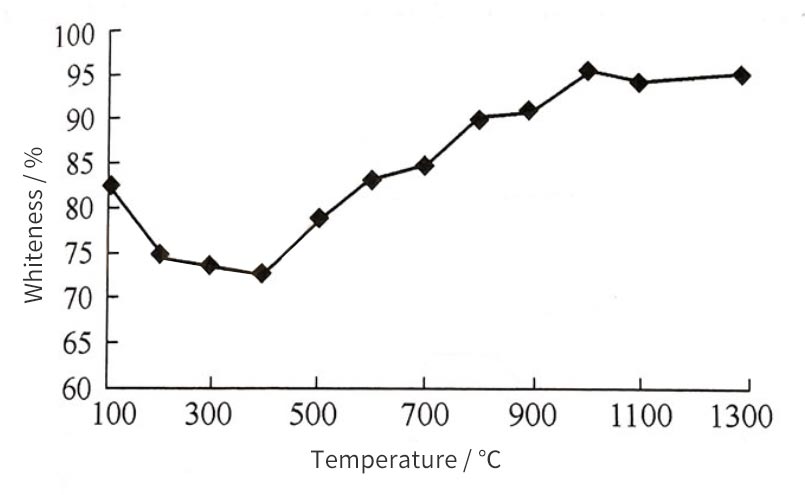
Ultra-fine grinding process of kaolin
In the deep processing of kaolin, in addition to whiteness, purity and other indicators, in order to meet the technical requirements of coated paper, coated paper, cardboard, as well as high-end paints and coatings, plastic box rubber products, etc., the particle size and fineness of kaolin products are very important. index of. At present, the ultra-fine technology with many high-end “double 90” products is basically becoming mature, and its processes are mainly divided into two types: dry method and wet method.
- Dry grinding process
Dry grinding is mostly used for ultra-fine grinding of hard kaolin or kaolin, especially for directly processing kaolin into ultra-fine powder that can meet user requirements. At present, the product fineness that can be achieved by dry production is generally D90≤10μm, that is, the final product is about 1250 mesh.
Dry ultra-fine grinding equipment is mostly jet mill, high-speed mechanical impact mill, vibration mill, etc.
In order to produce high-grade kaolin products, a two-stage ultra-fine grinding process can be used. The first stage uses an impact crusher, the second stage uses a jet crusher, plus certain grading equipment to obtain a product with a size of -2μm accounting for 80% to 90%. . In order to control the product size, especially the largest particle content, it is often necessary to configure fine grading equipment.
- Wet superfine grinding process
The ultra-fine grinding method must be used to produce paint-grade high-grade kaolin products with D90≤2μm during wet ultra-fine grinding.
Before the wet superfine grinding, the kaolin is pulped by a masher, and at the same time, it can be purified, whitened, and classified in the process, and then superfine grinding is carried out with equipment such as a peeling machine and a stirring mill. In order to make the product particle size D90≤2μm, multiple peeling machines can be used for multi-stage peeling and ultra-fine grinding during the ultra-fine grinding process.
Kaolin has flaky crystals, and ultra-flaky kaolin has excellent performance when used as a filler. Therefore, the wet ultra-fine pulverization of kaolin is also called peeling, which means that the thicker laminated kaolin is peeled off into thinner flakes, while maintaining Its original crystal characteristics. The peeling methods include wet grinding, squeezing and chemical soaking.
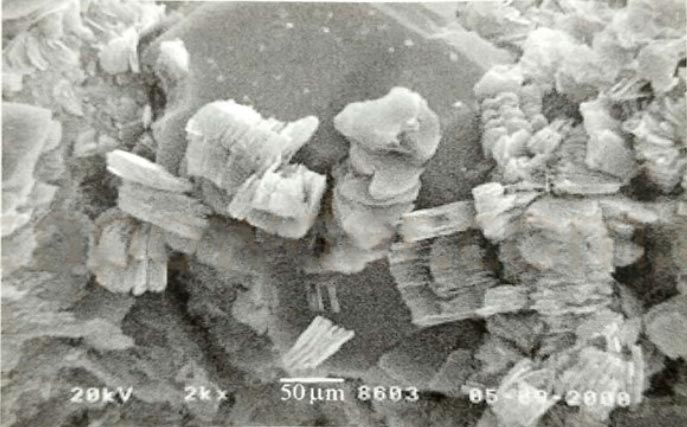
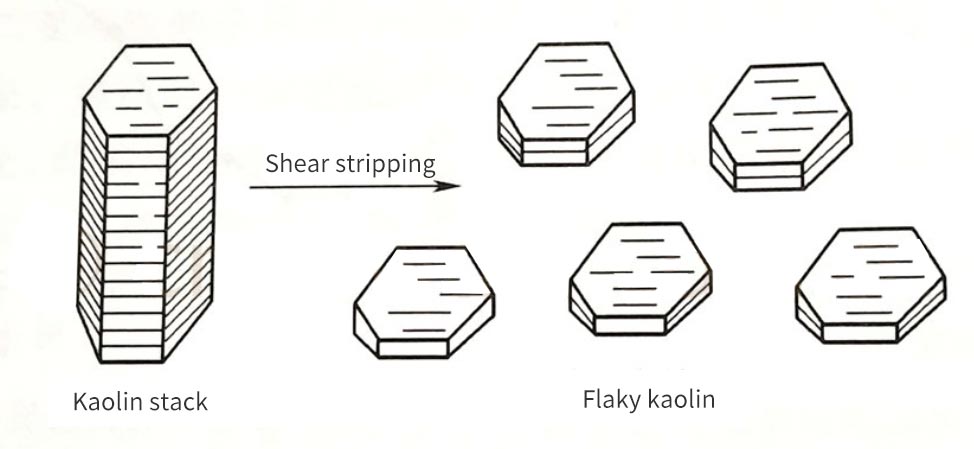
Article source: China Powder Network