Maintenance of air classifier equipment
Air current classifier is a kind of air classification equipment. The classifier, cyclone separator, dust collector and induced draft fan constitute a classification system. It has been widely used to purify quartz, feldspar, mica, kaolin, magnesium oxide, etc.
Under the action of the suction of the fan, the air flow classifier moves the materials to the classification area at a high speed from the inlet of the lower end of the classifier along with the upward air flow. Under the effect of the strong centrifugal force generated by the high-speed rotating classification turbine, the coarse and fine materials are separated. The fine particles that meet the particle size requirements enter the cyclone separator or dust collector through the gap between the grading wheel blades for collection.
After the coarse particles entrained by the air classifier collide with the barrel wall, the speed disappears and descends to the secondary tuyere along the barrel wall. Coarse particles and fine particles are separated by intense elution with secondary air. The fine particles rise to the classification zone for secondary classification, and the coarse particles fall to the discharge port for discharge.
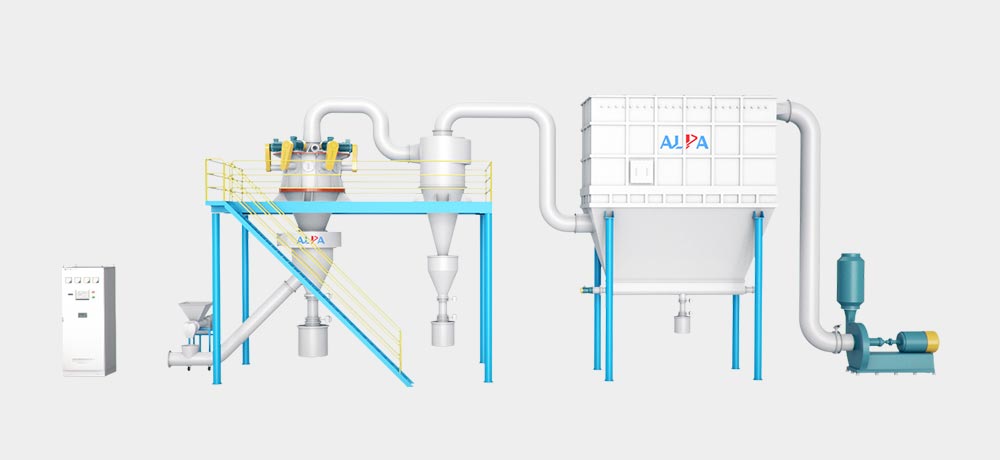
Machinery also needs constant protection from maintenance personnel. Practice has proved that the service life of equipment depends to a large extent on the quality of maintenance. In order to ensure the safe operation of equipment, the following are some common protection methods for air classifiers:
1. Before installing the air classifier, clean the pneumatic conveying pipeline with compressed air.
2. After the grading wheel has been running for a period of time (usually three months), the usage should be checked in time.
3. The motor should be placed in a well-ventilated place, and regularly check whether the cooling fan of the motor is working properly.
4. When starting the air flow classifier, it should be started slowly. The time from zero to working speed should generally not be shorter than 50 seconds.
5. If there is a problem with each pressure reducing valve, it should be replaced and repaired in time.
6. Thoroughly clean the vacuum cleaner, dust collection room and clean room in the open air at least once a year to avoid agglomeration and deposition.
7. All bearings should be smoothed and protected with lubricating oil regularly, and loose fasteners should be tightened in time to adjust the clearance of moving parts.