Application of jet pulverization equipment in the production of titanium dioxide
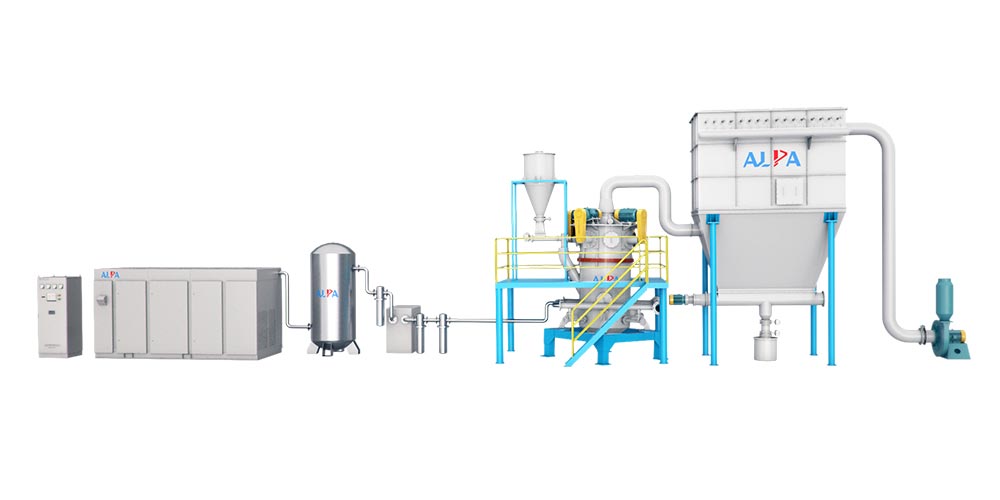
1. The principle of jet crushing
Jet milling equipment includes jet mill, jet mill or fluid energy mill, which uses the energy of high-speed airflow or superheated steam to make particles impact, collide, and rub against each other to achieve ultrafine pulverization or depolymerization. The general principle of jet milling: the dry and oil-free compressed air or superheated steam is accelerated into a supersonic airflow through the Laval nozzle, and the high-speed jet ejected drives the material to move at a high speed, causing the particles to collide and rub against each other and be crushed. The crushed materials arrive at the classification area with the airflow, and the materials that meet the fineness requirements are finally collected by the classifier, and the materials that do not meet the requirements are returned to the crushing chamber to continue crushing.
2. Classification of jet milling equipment
The jet mills used in industry mainly include the following types: flat jet mill, fluidized bed jet jet mill, circulating tube jet mill, counter jet jet mill, and target jet mill. Among these types of jet mills, flat jet mills, fluidized bed jet mills, and circulating tube jet mills are widely used.
2.1 Counter jet jet mill
After the material enters the crushing chamber through the screw feeder, the impact energy of the high-speed airflow is sprayed out by several relatively set nozzles, and the rapid expansion of the airflow forms the collision and friction generated by the suspension and boiling of the fluidized bed to crush the material. Coarse and fine mixed powder is driven by the negative pressure airflow through the turbine classification device installed on the top. The fine powder is forced to pass through the classification device and is collected by the cyclone collector and bag filter. The coarse powder is thrown away by gravity and the centrifugal force generated by the high-speed rotating classification device. It goes to the four walls and settles back to the crushing chamber to continue crushing.
2.2 Flat jet mill
The high-pressure airflow as the crushing kinetic energy enters the pressure-stabilized air storage bag on the periphery of the crushing chamber as an air distribution station. The airflow is accelerated into a supersonic airflow through the Laval nozzle and then enters the crushing chamber, and the material is accelerated into the crushing chamber through the Venturi nozzle. Perform simultaneous crushing. Since the Laval nozzle and the crushing chamber are installed at an acute angle, the high-speed jet stream drives the material to circulate in the crushing chamber, and the particles collide, collide, and rub against each other as well as with the wall of the fixed target plate to be crushed. Driven by the centripetal airflow, the fine particles are introduced into the central outlet pipe of the pulverizer and enter the cyclone separator for collection, while the coarse powder is thrown to the surrounding wall of the pulverization chamber under the action of centrifugal force for circular motion and continues pulverization.
2.3 Circulating tube jet mill
The raw material is fed into the crushing chamber through the Venturi nozzle, and the high-pressure air is sprayed into the runway-shaped circulating tubular crushing chamber with unequal diameter and variable curvature through a group of nozzles, accelerating the particles to collide, collide, rub and crush each other. At the same time, the swirling flow also drives the crushed particles upwards into the classification area along the pipeline, and the dense material flow is shunted under the action of the centrifugal force field in the classification area, and the fine particles are discharged after being classified by the louver type inertial classifier in the inner layer. Coarse particles return along the downpipe in the outer layer and continue to be pulverized in a circular manner.
2.4 Fluidized bed jet mill
Jet mill (fluidized bed jet mill) is the compressed air that is accelerated by the Laval nozzle into a supersonic airflow and then injected into the crushing area to make the material fluidized (the airflow expands to form a fluidized bed that suspends and boils and collides with each other). Therefore every particle has the same motion state. In the pulverization zone, the accelerated particles collide with each other and pulverize at the junction of each nozzle. The crushed material is conveyed to the classification area by the updraft, and the fine powder meeting the particle size requirement is screened out by the classifying wheels arranged horizontally, and the coarse powder not meeting the particle size requirement is returned to the crushing area for further crushing. Qualified fine powder enters the high-efficiency cyclone separator with the airflow to be collected, and the dusty gas is filtered and purified by the dust collector and then discharged into the atmosphere.
Application of jet pulverization equipment in the production of titanium dioxide
1. Titanium dioxide requirements for crushing
Titanium dioxide used as a pigment has excellent optical properties and stable chemical properties. Titanium dioxide has very high requirements on particle size, particle size distribution and purity. Generally, the particle size of titanium dioxide is based on the wavelength range of visible light, that is, 0.15m ~ 0.35m. And as a white basic pigment, it is very sensitive to the increase of impurities, especially iron impurities, and the increase is required to be less than 5 ppm when pulverized. In addition, titanium dioxide is also required to have good dispersibility in different coating systems. Therefore, the general mechanical crushing equipment is difficult to meet the requirements, so the final crushing of titanium dioxide (finished product crushing), at present, jet mills are used at home and abroad.
2. The choice of jet mill for titanium dioxide production
According to the crushing requirements of titanium dioxide: narrow particle size distribution, less increase in inclusions, good dispersibility, etc., and the material characteristics of titanium dioxide: high viscosity, poor fluidity, fine particle size and easy wall attachment, etc., currently titanium dioxide manufacturers all choose self-grading function The flat (also known as horizontal disc) airflow mill is used as the final crushing equipment for titanium dioxide;
And use superheated steam as crushing tool. Because the steam is easy to get and cheap, the pressure of the steam working medium is much higher than that of the compressed air and it is also easy to increase, so the kinetic energy of the steam is larger than that of the compressed air. At the same time, the cleanliness of superheated steam is higher than that of compressed air, with low viscosity and no static electricity. Moreover, while crushing, it can eliminate the static electricity generated by material collision and friction, and reduce the secondary cohesion of powdered materials. In addition, crushing at high temperature can improve the application dispersibility of titanium dioxide and increase the fluidity of titanium dioxide. The energy consumption of superheated steam is low, which is only 30% to 65% of that of compressed air.
3. Development of jet milling
With the rapid development of titanium dioxide industry, the requirements for equipment are getting higher and higher. On the premise of meeting the process conditions and quality requirements, the large-scale and systematization of equipment is particularly important, and jet milling is also constantly improving along with the development of titanium dioxide. The production capacity of the gas powder machine has also changed from the initial 1.2t/h to 1.5 t/h to 2.5 t/h to 3.5 t/h now, and the production capacity of the gas powder system has also changed from 10,000 t/h for a single line a. Up to now, the single line is 20,000 t/a, and the collection method has also changed from the relatively backward wet collection to the advanced dry collection, which greatly improves the primary yield and reduces waste.