What factors will affect the working efficiency of the jet mill
Jet mill is a device that uses high-speed airflow for grinding. After compressed air is filtered and dried, it is jetted into the grinding chamber at high speed through Laval nozzles. At the intersection of multiple high-pressure airflows, the materials are repeatedly collided, rubbed, and sheared to be crushed. .
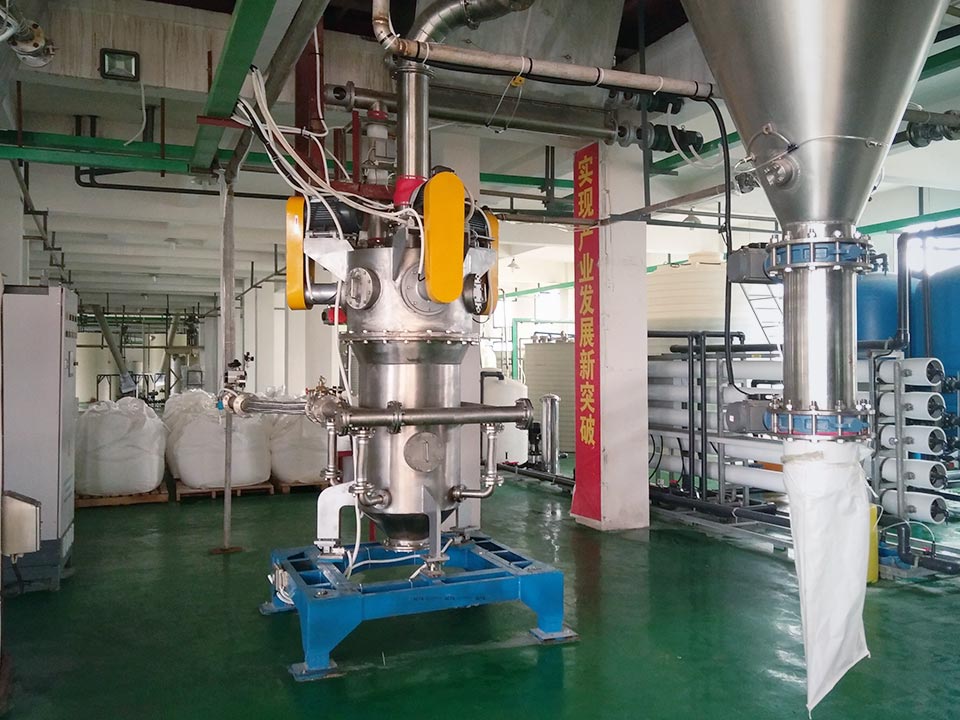
There are several factors that affect the working efficiency of the jet mill.
1. Material characteristics. Generally speaking, the jet mill can be adapted to the crushing of all brittle materials. However, due to the different properties of the materials, their crushing performance is also different. Due to the difference in the strength, density, hardness, viscosity, shape and electrical properties of various materials, the difference in grinding results is inevitably caused, and the strength of the material is an important factor. In addition, because the moisture content of water or oil in some materials or air sources is too high, the properties of the abrasive material (such as the increase in toughness and viscosity) will affect the fineness of the grinding.
2. Processing volume, the same material has different grinding fineness due to different processing volume. Generally speaking, the processing capacity is directly proportional to the particle size of the product. However, if the processing volume is too small, the chance of collisions between particles will be reduced, thereby affecting the fineness.
3. The influence of back pressure, the back pressure is the average pressure of the gas in the crushing chamber. Since the spray speed of the crushing nozzle is mainly determined by the difference between the nozzle inlet pressure and the outlet pressure, the greater the pressure difference, the greater the flow rate. Therefore, the increase in back pressure is not conducive to polishing. In production, the increase in the resistance of the capture system will increase the back pressure of the jet mill and affect the grinding effect of the powder. Therefore, be sure to check the resistance of the capture system.
Ultra-fine grinding of kaolin
The main mineral composition of kaolin is 90% kaolin + 10% halloysite, quartz, jellyfish stone, etc., commonly known as "china clay". The world's kaolin resources are rich and widely distributed. At present, the world has identified about 20.9 billion tons of kaolin resources. In the world, the Americas are the main producing areas of kaolin, and kaolin production accounts for about 35% of the world's total output; Europe's kaolin production has long been ranked second in the world, accounting for about 30% of the world's total output.
Kaolin is divided into hard kaolin, light kaolin and sandy kaolin.
Hard kaolin: hard (Mohs hardness 3~4), no plasticity, plasticity only after crushing and fine grinding. This kind of kaolin is dark gray, brown, etc. due to its high-quality impurities.
Lightweight kaolin: soft, generally strong plasticity, sand content <50%.
Sandy kaolin: soft, general plasticity, strong plasticity after sand removal, sand content ≥50%.
Kaolin is widely used and can be used in ceramic industry, paper industry, rubber industry, enamel industry, refractory material industry, environmental protection and chemical industry, etc.
Ceramic industry: mainly used for daily-use ceramics, architectural ceramics, sanitary ceramics, special ceramics and arts and crafts ceramics.
Paper industry: used as fillers and coatings for papermaking.
Rubber industry: used as a filling and reinforcing agent for rubber products.
Enamel industry: Kaolin with high whiteness, fine particle size and good suspension performance is used as silicate glass coating for enamel products.
Refractory industry: multi-clinker refractories, semi-acid refractories, etc.
Environmental protection and chemical industry: production of polyaluminum, treatment of industrial domestic water, production of alum, aluminum chloride and other chemical agents.
The whiteness of kaolin is one of the important indicators that determine its application value. The dyeing impurities in kaolin are mainly iron, titanium minerals and organic matter. Iron and titanium mostly exist in the form of hematite, goethite, pyrite, siderite and other minerals, and their distribution in kaolin is also very complicated, and most of the crystalline ones are mixed with fine particles. Since iron-containing minerals will become Fe2O3 when calcined at high temperatures, the raw materials will turn yellow or brick red. Therefore, measures to remove iron must be taken before or during calcination to increase the whiteness of the product to 92% or higher.
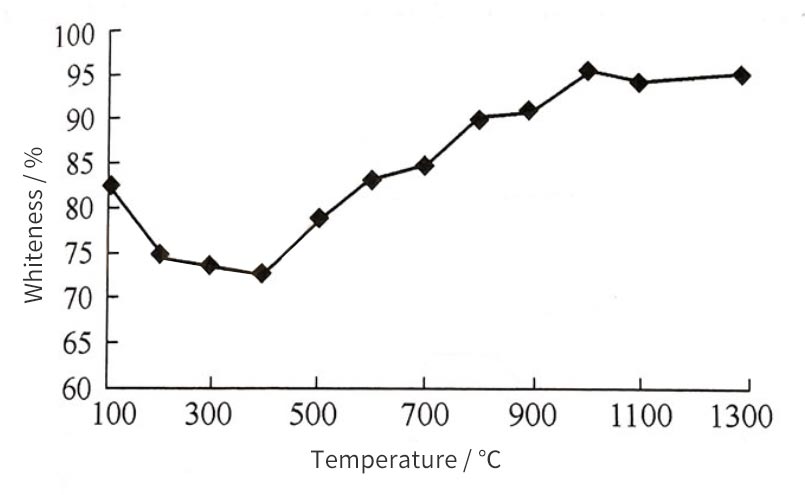
Ultra-fine grinding process of kaolin
In the deep processing of kaolin, in addition to whiteness, purity and other indicators, in order to meet the technical requirements of coated paper, coated paper, cardboard, as well as high-end paints and coatings, plastic box rubber products, etc., the particle size and fineness of kaolin products are very important. index of. At present, the ultra-fine technology with many high-end "double 90" products is basically becoming mature, and its processes are mainly divided into two types: dry method and wet method.
- Dry grinding process
Dry grinding is mostly used for ultra-fine grinding of hard kaolin or kaolin, especially for directly processing kaolin into ultra-fine powder that can meet user requirements. At present, the product fineness that can be achieved by dry production is generally D90≤10μm, that is, the final product is about 1250 mesh.
Dry ultra-fine grinding equipment is mostly jet mill, high-speed mechanical impact mill, vibration mill, etc.
In order to produce high-grade kaolin products, a two-stage ultra-fine grinding process can be used. The first stage uses an impact crusher, the second stage uses a jet crusher, plus certain grading equipment to obtain a product with a size of -2μm accounting for 80% to 90%. . In order to control the product size, especially the largest particle content, it is often necessary to configure fine grading equipment.
- Wet superfine grinding process
The ultra-fine grinding method must be used to produce paint-grade high-grade kaolin products with D90≤2μm during wet ultra-fine grinding.
Before the wet superfine grinding, the kaolin is pulped by a masher, and at the same time, it can be purified, whitened, and classified in the process, and then superfine grinding is carried out with equipment such as a peeling machine and a stirring mill. In order to make the product particle size D90≤2μm, multiple peeling machines can be used for multi-stage peeling and ultra-fine grinding during the ultra-fine grinding process.
Kaolin has flaky crystals, and ultra-flaky kaolin has excellent performance when used as a filler. Therefore, the wet ultra-fine pulverization of kaolin is also called peeling, which means that the thicker laminated kaolin is peeled off into thinner flakes, while maintaining Its original crystal characteristics. The peeling methods include wet grinding, squeezing and chemical soaking.
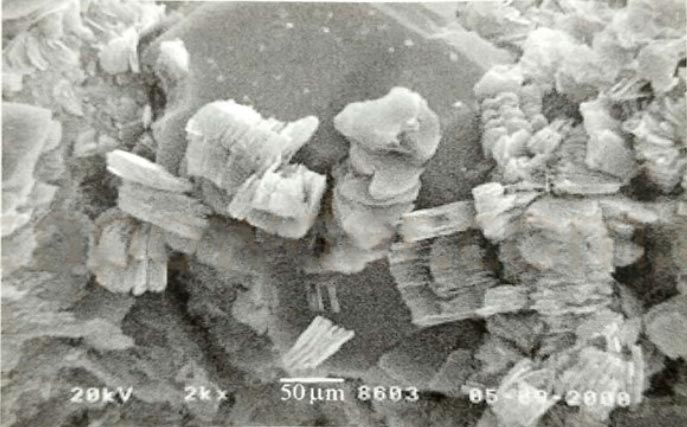
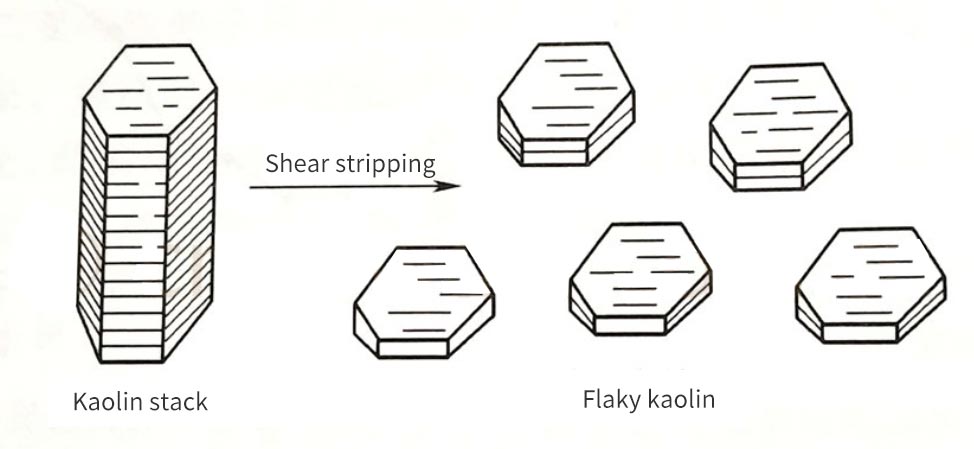
Article source: China Powder Network
How to extend the service life of jet mill
After working for a long time, how to update and maintain the jet mill to make its lifespan longer, bring more benefits to manufacturers and save energy.
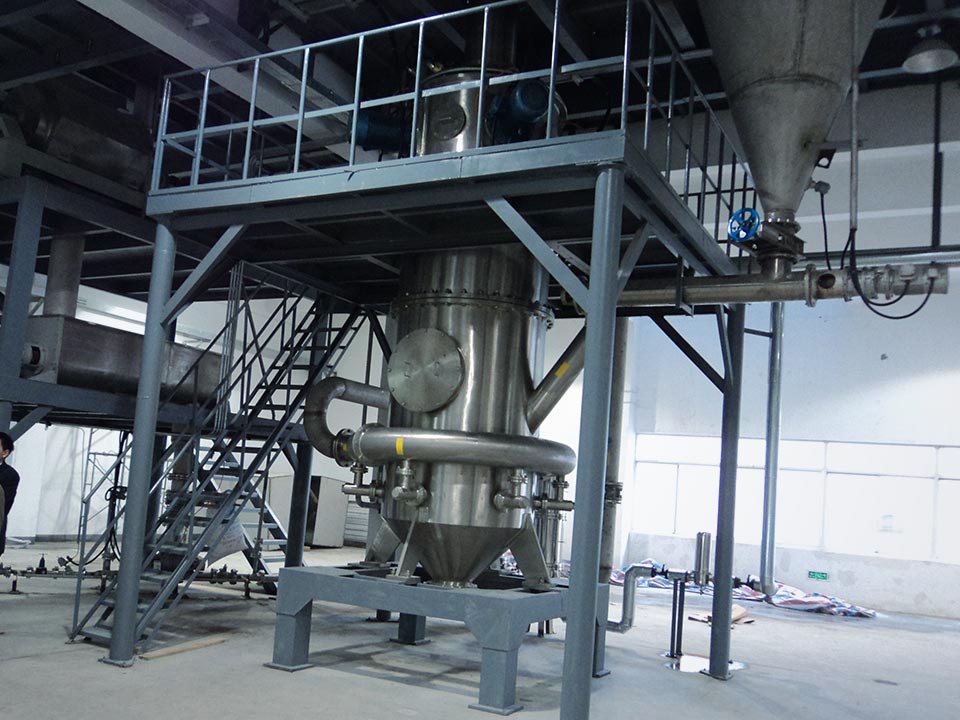
(1) The jet mill will accumulate a lot of dust under long-term work. How to clean it at this time? When cleaning it, the motor and bearings cannot be wetted. The all-ceramic grinder adopts advanced grinding technology and manufacturing level. It is a high-efficiency equipment for grinding hard and abrasive materials. It is especially suitable for grinding highways, railways, airport runways and other engineering buildings. Highways, railways, airport runways and other engineering stones are mostly hard rock such as basalt, with specifications of 3-7 cm or 2-8 cm, and the hardness of the crushed materials is relatively large. General grinders are not only low in output but also easy to wear. .
(2) When replacing parts or performing updates and maintenance, work must be performed under power-off conditions, and prominent warning signs should be hung up.
(3) Lubricate the machine in time to make it more efficient.
(4) Lubricating oil must be added after the working time of the general classification part is 1500 hours.
(5) When the open-air work is completed, the interior must be cleaned and cleaned. Cover it with fireproof cloth and rainproof cloth to prevent internal machinery from rusting. It must be fireproof and waterproof with multiple precautions.
(6) If there is a sudden stop of work, the power must be turned off first, and we are performing maintenance after the power is off. When the machine is running, the body should be locked and it is strictly forbidden to open it.
(7) When the machine is working normally, it must be equipped with belts for installation safety protection to prevent personal safety.
Some of the above methods are measures that can extend the life of the jet mill. The all-ceramic crusher is a new type of fine grinding and coarse grinding product developed by optimizing the main technical parameters. It has the characteristics of large grinding ratio, low energy consumption, stable operation, simple structure, convenient operation and maintenance, etc. It is a truly multi-purpose, A new type of high-efficiency, low-cost grinding equipment.
Application of diatomite
Diatomaceous earth is a kind of biochemical sediment, mainly formed by the accumulation of fossil bone remains of single-celled plant algae in ancient geological period, and is a non-renewable natural resource. Its main mineral composition is opal and its variants, and its chemical composition is mainly SiO2, and contains a small amount of Al2O3, Fe2O3, CaO, Na2O, MgO, etc.
Diatomaceous earth is commonly known as mountain powder, fossil powder or radiolarian powder. It is an important high-efficiency non-metallic mineral. It has many advantages such as large porosity and strong adsorption. It can be used in building materials, light industry, chemical industry, petroleum, food grade and environmental protection field.
Pure diatomaceous earth is generally in the form of white soil. When it contains impurities, it is often polluted by iron oxides or organic matter and becomes gray, yellow, green, and black. Most diatomaceous earth is light, porous and easily broken, but the hardness of the diatomaceous earth bone particles is relatively large. The density of diatomaceous earth is very small, the average bulk density: 0.66g/cm3, thermal stability: After the original soil is calcined at 900℃ for 2h, the regularly arranged pore structure of the diatom shell wall remains intact. When it is calcined at 1200℃ for 2h, then The arrangement of diatom pores will be destroyed.
The particle structure of diatomaceous earth is closely related to diatoms. The individual diatoms are small, generally 1~100μm. The mineral composition of diatom remains is amorphous SiO2, which has good chemical stability and is thermal, acoustic and electrical of poor conductors.
The chemical composition of diatomaceous earth is mainly silicate, and the level of silica content is an important indicator to measure the quality of diatomaceous earth. It can be divided into high-grade diatomaceous earth and inferior diatomaceous earth.
Diatomaceous earth is a solid acid, which is weakly acidic. In addition to being soluble in hydrofluoric acid, it is insoluble in other acids and can react with weak bases. Its surface adsorption properties are related to its surface structure. The surface of diatomaceous earth is covered by a large number of silyl hydroxyl groups, and there are hydrogen bonds. OH groups are also distributed on the inner surface of the pores of the diatomaceous earth.
Diatomite is rich in resources and widely distributed around the world, mainly distributed in 122 countries and regions such as the United States, China, Argentina, Peru, Denmark, and Japan. However, the resource grade and economic value are high, and the mineral deposits that can be directly developed and utilized are not many. At present, dozens of countries and regions produce diatomite products with an annual output of hundreds of tons. The largest output is the United States, followed by Russia, France and Germany.
Application of diatomite
- Filter aid
Filter aid is a granular material with uniform particles, hard properties and small compressibility. Its function is to filter and separate small particles and prevent colloidal particles from clogging the medium. The most widespread use of diatomaceous earth is as a filter aid for separating suspended solids in liquids. The reason why diatomaceous earth is suitable as a filter aid is that it has poor solubility, suitable particle size distribution and porous structure.
- Application in building materials industry
(1) Application of diatomite in interior wall coatings
The diatom mud made of diatomite as a raw material is used in interior decoration coatings, especially interior wall coatings, and has very good effects on the purification of indoor air and the adjustment of temperature and humidity.
(2) Application of diatomite in environmental protection wall materials
Due to the unique physical structure of diatomite, the diatom mud can fully absorb the formaldehyde and benzene present in the air, and it also has a great promotion effect on indoor air purification, which is very helpful to keep the indoor air fresh.
(3) Application of diatomite in concrete
An obvious application of diatomite in the building materials industry is concrete. Determined by the nature of diatomaceous earth, the surface of diatomaceous earth is rough, and it has strong advantages in high temperature resistance and corrosion resistance. When used with asphalt materials, it can effectively improve the quality of concrete.
(4) Application of diatomite in lightweight wall materials
Diatomite is used in lightweight wall materials and has great advantages in plasticity and sintering molding. After processing, the hardness is also greatly improved. This is due to the fact that there are many pores on the surface of diatomaceous earth, which can allow other materials to merge into the pores. After processing, the wall can be insulated and the weight is greatly reduced.
- Catalyst carrier
Diatomaceous earth is inert to most chemical reactions and resistant to high temperatures, so it can be used as an ideal catalyst carrier. Generally used as a catalyst for chemical reactions such as oxidation, hydrogenation, dehydrogenation, hydration, and reduction. For example, the nickel catalyst in the hydrogenation process, the vanadium catalyst in the preparation of sulfuric acid, the phosphorus catalyst used in petroleum refining, and the catalyst for automobile exhaust gas treatment can all be supported by diatomaceous earth.
- Adsorbent
Diatomaceous earth adsorbent is mainly used for the decolorization and refining of mineral oil, animal and vegetable oils, adsorbing and removing asphaltenes, neutral collagen, sulfide olefins, naphthenic acid, minerals, carotene, lutein, chlorophyll, etc.
Article source: China Powder Network
The difference between open-circuit jet mill and closed-circuit jet mill
Jet mill is a kind of micron level ultra-fine grinding equipment, which is more common in various powder industries. The jet mill has two different structures, divided into open-circuit and closed-circuit. The open circuit system usually refers to the use of air as a medium to crush, filter and discharge after crushing. The closed-circuit system refers to the use of inert gas as the medium. The materials in the system are under the protection of inert gas during the entire process of feeding, crushing, grading, conveying, separating and packaging. After dust removal and filtration, the inert gas is returned to the front-end system for recycling.
1. Open-circuit jet mill
Jet mill (fluidized bed jet mill) is the compressed air accelerated by Laval nozzle into supersonic air flow and then injected into the crushing zone to make the material fluidized (air flow expands into fluidized bed suspension boiling and collides with each other), so Each particle has the same state of motion. In the crushing zone, the accelerated particles collide and crush at the intersection of the nozzles. The crushed materials are transported to the grading area by the ascending airflow, and the fine powder that meets the particle size requirements is screened out by the grading wheel, and the coarse powder that does not meet the particle size requirements is returned to the crushing area to continue pulverization. The qualified fine powder enters the high-efficiency cyclone separator along with the air flow and is collected, and the dust-containing gas is filtered and purified by the dust collector and then discharged.
2. Closed-circuit jet mill
The closed-circuit jet mill generally refers to the air jet mill based on the air outlet of the pulse dust collector connected with the air inlet of the air compressor that provides the power source of the system to form a closed system to make the smashing medium of the entire pulverization process ( Air or inert gases such as nitrogen, argon, helium, carbon dioxide, etc.) circulate in a closed system.
The closed-circuit jet mill is a closed-circuit jet pulverization system developed for the crushing requirements of special materials such as flammable, explosive, easy to oxidize, and volatile. It is protected by inert gas circulation. The working process is that the cooled inert gas is accelerated by the Laval nozzle into a supersonic airflow and sprayed into the central crushing area of the pulverizer. The sonic airflow brings the animal material to collide with each other in the crushing area to achieve the goal of crushing. The crushed material enters the classification area with the updraft, and the powder material that meets the particle size requirements is sorted by the classification wheel in the classification area. The particle size of the powder is sorted by adjusting the speed of the grading wheel. The sorted products are discharged from the centrifugal separator along with the airflow or collected after being filtered by the dust collector. The unqualified ones continue to return to the crushing area for two Smashed. The filtered inert gas is compressed and recycled by the compressor system, and the whole process is automated.
The open-circuit jet mill can be used for the processing of most common powder materials, and the closed-circuit jet mill is mainly used for flammable, explosive, and oxidizable raw materials. The user can choose according to the raw materials and processing requirements.
Performance of Titanium Dioxide & Its Function and Application in Coatings
Titanium dioxide pigments are divided into two types: anatase type and rutile type. According to international practice, they are called R type and A type respectively. The rutile type and anatase type without post-treatment are called RI type and AI type respectively; the rutile type and anatase type after the post-treatment are called R2, R3 and A2 type respectively. At present, most of the rutile titanium dioxides on the market belong to R2 and R3 types, of which R2 type accounts for more than 70% of sales. R2 and R3 account for 77% and 22% of rutile titanium dioxide for coatings, respectively.
Performance and use of pigment grade titanium dioxide
Pigment-based titanium dioxide has high refractive index, strong achromatic power, large hiding power, good dispersibility, good whiteness, non-toxic, stable physical and chemical properties, and excellent optical and electrical properties, so it has a wide range of uses , Paint, plastic, paper, chemical fiber, ink, rubber, cosmetics, etc. all use pigment-grade titanium dioxide. Among them, the largest amount is paint, accounting for about 57%. In particular, rutile titanium dioxide is mostly consumed by the coating industry. With the rapid rise of China's automobile industry, construction industry and water-based coatings, the coating industry not only needs more titanium dioxide in quantity, but also has higher quality requirements and more varieties.
The refractive index of rutile titanium dioxide is 2.76, and the refractive index of anatase titanium dioxide is 2.55. The hiding power is determined by the difference between the refractive index of the pigment and the refractive index of the medium, and their relative values can be calculated according to the formula. The reflection coefficient of rutile titanium dioxide is 25% to 30% higher than that of anatase titanium dioxide, which means that if it produces the same hiding power as anatase titanium dioxide, the amount of rutile titanium dioxide can be reduced by 25% to 30%. In addition, rutile titanium dioxide has a compact structure, relatively stable, low photochemical activity, resistance to ultraviolet light, is not easy to pulverize outdoors, and has better weather resistance and gloss than anatase titanium dioxide. Therefore, it is widely used in various outdoor coatings with high weather resistance for high-grade ships, bridges, automobiles, buildings, etc., which accounts for about 70% of the coatings. Anatase titanium dioxide is easy to pulverize and yellow, so it is generally only used For indoor coatings or primers, the amount only accounts for 30% of the titanium dioxide used in coatings.
The role of pigment grade titanium dioxide in coatings
Coatings are viscous suspensions composed of base materials, pigments, fillers, solvents and additives. It is coated on the surface of the object to form a tough coating film, which plays a role of decoration and protection on the object.
Regardless of solvent-based or water-based coatings, if titanium dioxide is used, its role is not only to cover and decorate, but also to improve the physical and chemical properties of the coating, enhance chemical stability, and even improve hiding power, color reducing power, and corrosion resistance., Light resistance, weather resistance, enhance the mechanical strength and adhesion of the paint film, prevent cracks, prevent the penetration of ultraviolet rays and moisture, thereby delaying aging and extending the life of the paint film. At the same time, it can save materials and increase varieties.
Regardless of solvent-based or water-based coatings, if titanium dioxide is used, its role is not only to cover and decorate, but also to improve the physical and chemical properties of the coating, enhance chemical stability, and even improve hiding power, color reduction power, and corrosion resistance. , Light resistance, weather resistance, enhance the mechanical strength and adhesion of the paint film, prevent cracks, prevent the penetration of ultraviolet rays and moisture, thereby delaying aging and extending the life of the paint film. At the same time, it can save materials and increase varieties.
Among the pigments, white pigments are the most widely used. Both white paints and light-colored paints use it. Therefore, the amount of white pigments used in paint production is much more than other pigments. The white pigments commonly used in coatings include zinc white, lithopone, titanium white and so on. Because some synthetic resin coatings have a high degree of polymerization, if zinc white is added, the zinc white will have a tendency to thicken due to its alkalinity and anti-acid effect with the free fat in the coating; if zinc white is added, the weather resistance will be poor. But the use of titanium dioxide can improve the above shortcomings. Because the titanium dioxide particles are small and uniform, and the photochemical stability is high, in terms of hiding power, rutile titanium dioxide is 7 times that of zinc white and 5.56 times that of lithopone, and anatase titanium dioxide is 5.57 times that of zinc white. Lithopone is 4.3 times; in terms of decoloring power, rutile titanium dioxide is 8.3 times that of zinc white and 6.25 times that of lithopone. Anatase type titanium dioxide is 6.4 times that of zinc white and 4.8 times that of lithopone. Times. In terms of use effect, 1t of titanium dioxide is at least equivalent to 4t of lithopone; in terms of service life (referring to outdoor chalking resistance), the coating with titanium white as a pigment is 3 times higher than that with lithopone as a pigment. Therefore, the use of titanium dioxide can greatly reduce the amount of pigments in the entire coating, and the coatings made are bright in color, not easy to yellow, light resistance, heat resistance, abrasion resistance, weather resistance, alkali resistance, sulfur resistance, and dilute acid resistance. It is precisely because titanium white has superior performance than zinc white and lithopone, it has become the best white pigment indispensable in paint production. The amount of titanium dioxide accounts for more than 90% of the total amount of pigments used in coatings, and more than 95% of the total amount of white pigments used in coatings. It accounts for 10% to 25% of the cost of coating raw materials.
Article source: China Powder Network
Ultra-fine grinder helps the development of lithium battery materials
The ultra-fine grinder has a uniquely designed grading chamber and a grading wheel with frequency conversion speed regulation. It does not need to be equipped with a screen and can classify the product size at a low speed. The circulating feed structure not only strictly limits the "large particles", but also avoids excessive crushing, so the product has a narrow particle size distribution. The classification wheel is used for classification, which avoids the difficulty of passing the powder with more than 150 mesh.
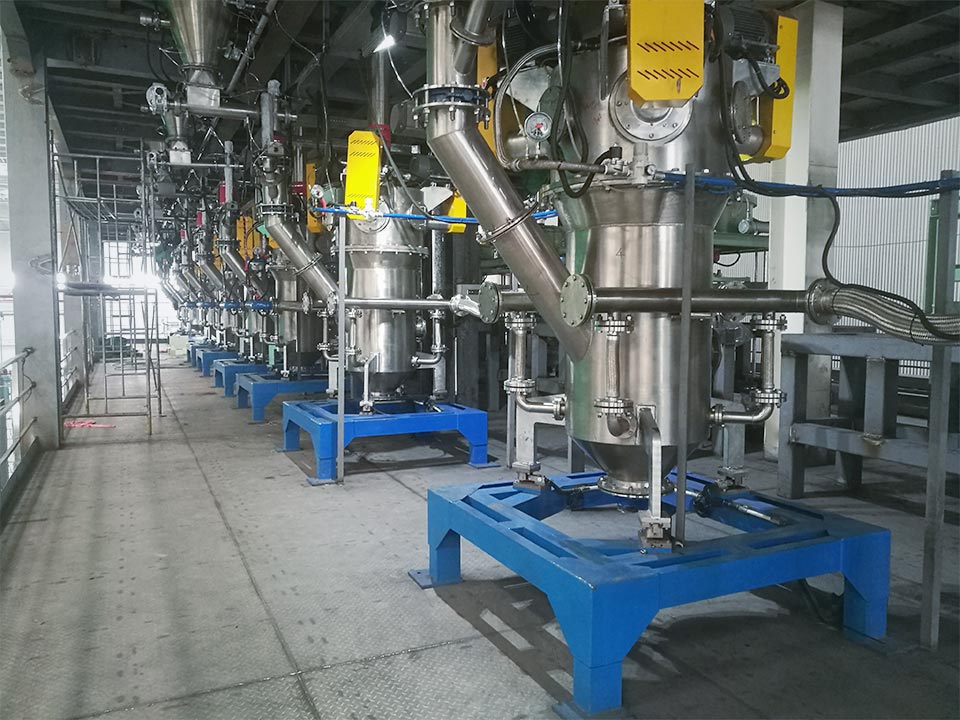
The main wear parts of the ultra-fine grinder: flat teeth, round teeth, large and small grinding teeth. The flat teeth and round teeth are made of stainless steel and have a good dynamic balance. If they are severely worn, they should be replaced. The size of the self-made metal processing should be specified, and the weight difference of each piece shall not exceed 1g to avoid vibration damage to the bearing and the machine.
At present, ultra-fine grinders have been used in batches for the cathode materials of lithium batteries, mainly including lithium cobalt oxide, lithium nickel oxide, lithium manganate, lithium nickel cobalt manganate (ternary material) and lithium iron phosphate. The crushing of the cathode material is a very critical process. Currently, commonly used equipment includes jet mills, mechanical mills, and sand mills.
As the capacity of the lithium-ion battery increases, the internal energy stored increases, and the internal temperature will increase. In severe cases, a short circuit may occur, thereby damaging the battery. Coating high-purity ultra-fine alumina on the surface of PP, PE or multilayer composite diaphragm can improve the safety of lithium-ion batteries.
What is the working principle of the ultra-fine grinder? The high-speed airflow generated by the air source system enters the pulverizing system, causing the material to rotate at a high speed, and the material collides with the material to achieve the purpose of ultra-fine pulverization. When materials enter the grading system, only materials that meet the particle size requirements will be collected, and those that do not meet the particle size requirements will be sent back to the crushing chamber to continue crushing. Repeat this process until the material meets the standard. The ultra-fine grinder can be used for the pulverization of chemical raw materials and non-metallic minerals.
Ultrafine grinding of dry and hard solid materials
In the modern industry, there are many follow-up products that require ultra-fine grinding of materials, such as black tea, ultra-fine grinding of tea leaves, such as ultra-fine grinding of rice husk powder, used to make special bags; ultra-fine grinding of silicon carbide, Used in various industries, etc., etc., are inseparable from the ultra-fine grinder.
The modern ultrafine grinder can set different types of pulverization for different materials, and can also customize different sizes of ultrafine grinder according to the size of the output. This modern ultrafine grinder has large output, low noise, convenient cleaning, sturdiness and durability. It is in line with the current trend of ultrafine grinding of materials and has become the new darling of current fashion.
The ultra-fine grinder is especially suitable for ultra-fine grnding of dry materials and hard materials. The grinding process is finer and the output is larger. The hard carbon powder structure of diamond can be ultra-finely pulverized, and the requirements of modern ultra-fine grinder for materials are as dry as possible.
The ultra-fine grinder is completely carried out in a closed environment when performing ultra-fine grinding, will not produce dust spills, and protect the working environment of workers. It is a very environmentally friendly mechanical equipment. According to the different grinding media, the ultrafine grinder is divided into jet pulverizer and mechanical grinder. The jet mill can be filled with air or special gas for ultra-fine grinding to ensure the integrity of the material. The mechanical crusher can be divided into many types, small rod crushing, etc. The specific principle is to perform ultrafine crushing through the collision of materials and equipment. However, no matter what kind of ultrafine grinder, it is very environmentally friendly in the process of grinding materials. The output can range from one catty to more than 100 catties per hour, and the fineness varies from a few hundred meshes to thousands of meshes.
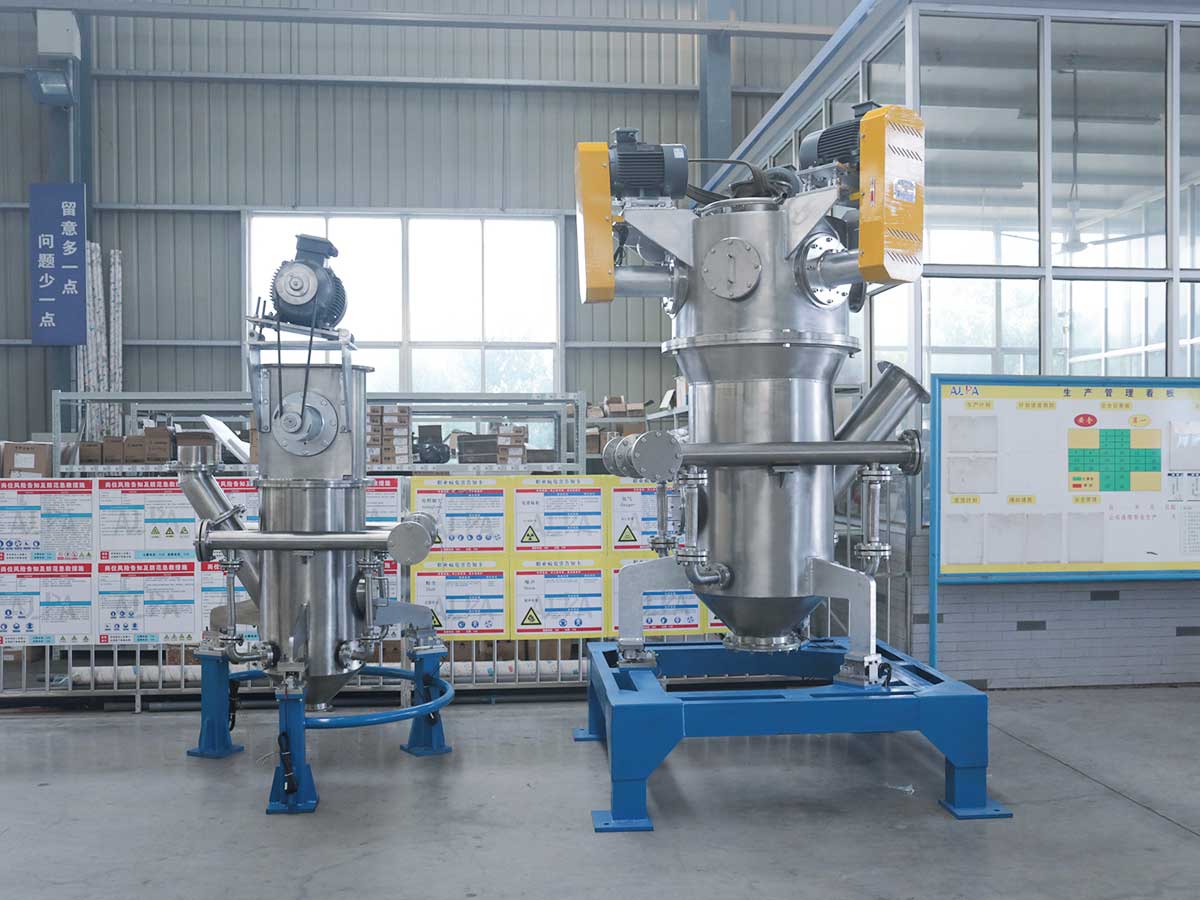
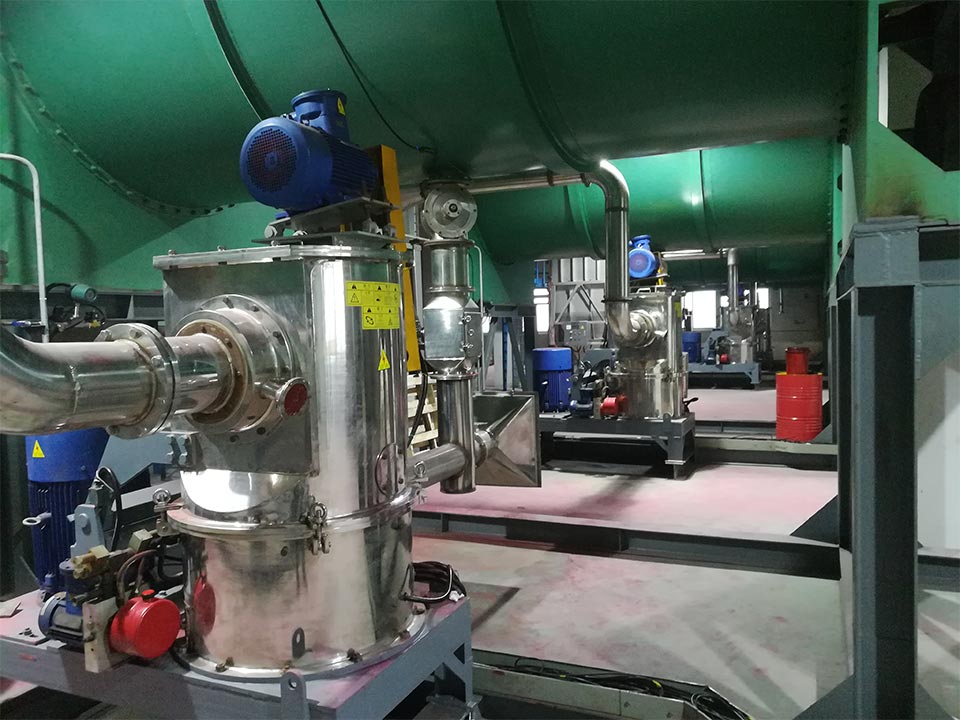
With the development of the times, ultra-fine grinders are used in chemical, mining, abrasives, refractory materials, battery materials, metallurgy, building materials, pharmaceuticals, ceramics, food, feed, new materials and other industries and the ultra-fine grinding of various dry powder materials. Dispersion and other aspects have been widely used. It is suitable for dry grinding of various materials with Mohs hardness below 9 and is especially suitable for the grinding of materials with high hardness, high purity and high added value. The crushed material has good particle shape and narrow particle size distribution.
Features and application of silicon powder
Silicon micropowder is made of natural quartz (SiO2) or fused quartz (amorphous SiO2 after high temperature melting and cooling of natural quartz) after crushing, ball milling (or vibration, jet milling), flotation, pickling purification, high-purity water treatment, etc. The micro powder processed by this technology. Silica powder is a non-toxic, odorless, non-polluting inorganic non-metallic material.
Physical and chemical properties
1. The appearance of silica powder is gray or off-white powder, and its refractoriness is >1600°C. Bulk density: 200~250 kg/m3.
2. The fineness of silica fume: more than 80% of the silica fume has a fineness of less than 1 micron, the average particle size is 0.1-0.3 microns, and the specific surface area is 20-28m2/g. Its fineness and specific surface area are about 80-100 times that of cement and 50-70 times that of fly ash. Common specifications for quartz powder are 400 mesh, 800 mesh, 1000 mesh, 1500 mesh and 2000 mesh.
3. Particle morphology and mineral phase structure: During the formation process of silica fume, due to the effect of surface tension during the phase transition, amorphous spherical particles of amorphous phase are formed, and the surface is relatively smooth, and some have multiple circles. An agglomerate of spherical particles sticking together. It is a kind of volcanic ash material with large specific surface area and high activity. For materials mixed with silica fume, tiny spheres can play a lubricating effect.
Silica powder can fill the pores between cement particles, and at the same time form a gel with the hydration product, and react with the alkaline material magnesium oxide to form a gel. In cement-based concrete, mortar and refractory castables, mixing a proper amount of silica fume can play the following role:
1. Significantly improve the compressive, flexural, impermeable, anti-corrosion, impact and wear resistance properties.
2. It has the functions of retaining water, preventing segregation and bleeding, and greatly reducing the resistance of concrete pumping.
3. Significantly prolong the service life of concrete. Especially in harsh environments such as chloride pollution erosion, sulfate erosion, and high humidity, the durability of concrete can be doubled or even several times higher.
4. Significantly reduce the floor ash of sprayed concrete and castables, and increase the thickness of a single sprayed layer.
5. It is a necessary component of high-strength concrete, and C150 concrete has been applied in engineering.
6. It has about 5 times the effect of cement. It can reduce costs and improve durability when used in ordinary concrete and low-cement castables.
7. Effectively prevent the occurrence of concrete alkali aggregate reaction.
8. Improve the compactness of castable refractories. When coexisting with Al2O3, it is easier to form mullite phase, which increases its high-temperature strength and thermal shock resistance.
Application field
1. Used in mortar and concrete: high-rise buildings, seaports, reservoirs and dams, water conservancy, culvert gates, railways, highways, bridges, subways, tunnels, airport runways, concrete pavements and coal mine tunnels, etc.
2. In the material industry:
- High-grade, high-performance, low-cement refractory castables and prefabricated parts have a service life three times that of ordinary castables. The refractoriness is increased by about 100°C, and the high-temperature strength and thermal shock resistance are significantly improved. Has been widely used in: coke oven, ironmaking, steelmaking, steel rolling, non-ferrous metals, glass, ceramics and power generation industries.
- Large iron trenches and ladle materials, air-permeable bricks, smear repair materials, etc.
- Construction application of self-flowing refractory casting material and dry-wet spraying.
- Oxide-bonded silicon carbide products (ceramic kiln furniture, flame screens, etc.).
- High temperature type calcium silicate light-weight thermal insulation material.
- The corundum mullite push plate is used for the electric porcelain kiln.
- High temperature wear-resistant materials and products.
- Corundum and ceramic products.
- Sialon combined products.
At present, in addition to being widely used in castable refractories, it has also been widely used in fused and sintered refractories.
3. New wall materials and facing materials:
- Polymer mortar, thermal insulation mortar and interface agent for wall insulation.
- Cement-based polymer waterproof material.
- Lightweight aggregate thermal insulation and energy-saving concrete and products.
- Putty powder processing for interior and exterior wall construction.
4. Other uses:
- Silicate brick material.
- Production of water glass.
- Used as a reinforcing material for organic compounds. Because its composition is similar to that of white carbon black produced by gas phase method. It can be used as a filling and reinforcing material in polymer materials such as rubber, resin, paint, paint, unsaturated polyester, etc.
- Used as an anti-caking agent in the fertilizer industry.
Article source: China Powder Network
Chinese medicine ultrafine pulverization technology
Regarding the ultrafine grinding of traditional Chinese medicine, researchers have given different names and concepts from different research perspectives, such as ultrafine Chinese medicine particles, single-flavored Chinese medicine ultrafine pieces, and ultrafine Chinese medicine powders. Since the effective ingredients of plant medicine and animal medicine are mainly distributed in the cell and intercellular substance, and mainly in the cell, some people refer to the pulverization for the purpose of breaking the cells of Chinese medicinal materials as the "cell-level micro pulverization" of Chinese medicine. The traditional Chinese medicine powder obtained by the micro-grinding method is called "cell-grade Chinese medicine powder". Similarly, the traditional Chinese medicine prepared on the basis of cell-grade Chinese medicine powder is called "cell-grade Chinese medicine", or "micro-powder Chinese medicine" for short.
Some people call powders with a particle size greater than 1μm as "fine powder", and fine powders with a particle size less than 1μm as "ultrafine powder". In fact, in terms of the particle size of traditional Chinese medicines, micro and nano traditional Chinese medicines that are currently in the ascendant of research are also classified as ultra-micro preparations of traditional Chinese medicines. Lu Fuer et al. believe that "micron Chinese medicine preparations" belong to cell-grade micropowder preparations, which are a new dosage form developed by using modern high-tech and traditional processing and preparation techniques. Generally, the particle size should be 1-75μm. Traditional Chinese medicines within the scope can maintain the inherent pharmacodynamic material basis of traditional Chinese medicines. "Micron Chinese medicine" includes micron Chinese medicinal materials, micron extracts of Chinese medicines, and micron Chinese medicine preparations, which increase the cell wall breakage rate of Chinese medicinal materials by more than 90%. The so-called "nano Chinese medicine" refers to the effective ingredients, effective parts, original medicines, and compound preparations of traditional Chinese medicines with a particle size of less than 100nm manufactured by the application of nanotechnology. It is a kind of Chinese medicine powder after nanometerization. According to the above point of view, some researchers divide the ultrafine powder into micron level (>1μm), submicron level (0.1-1μm) and nano level (1-100nm), and divide the ultrafine powder technology into micron technology. , Submicron technology and nanotechnology.
Judging from the current research progress, although there are many names of Chinese medicine ultrafine grinders, related concepts and connotations are not the same, most of them think that the ultrafine grinding of Chinese medicine refers to the cell-level pulverization of Chinese medicine. The particle size is below 75μm. With the continuous deepening of research work, the definition or concept of ultrafine grinding of traditional Chinese medicine will be more scientific and accurate.
The Chinese medicine ultrafine grinder has a high cell wall breaking rate, which is conducive to the release and absorption of drugs. Ordinary crushed medicinal powder has a low rate of cell wall breaking. When the medicine enters the body, the powder particles of the medicinal powder absorb water and expand, and the active ingredients are continuously released from the cell wall and cell membrane through diffusion. Diffusion requires a concentration difference between the inside and outside of the cell. When the concentration difference between the inside and outside of the cell is small or balanced, the release rate of the active ingredient will be very slow or even stop. The active ingredient located in the inner cell is sometimes excreted before it can be released, so it is often not reached. To an effective therapeutic concentration.
After the Chinese medicine ultrafine grinder, the cell wall breakage rate is high, and the active ingredients are exposed before entering the body. After entering the body, the soluble ingredients are quickly dissolved. Great adhesion and tightly adhere to the mucosa of the inner wall of the gastrointestinal tract, so that the residence time in the gastrointestinal tract is prolonged, the absorption is more sufficient, and the absorption amount will increase. Since most of the cell wall is destroyed during crushing, the effective ingredients do not need to pass through the cell wall and cell membrane release process. In this way, ultrafine pulverization is far superior to ordinary pulverization in terms of drug release speed and release amount. Mineral medicine can reach micrometers even after ultra-fine grinding, which is conducive to the absorption of medicine and the improvement of curative effect.