Advantages and disadvantages of different sealing methods of air classifier
Air classifier is the key to the production of ultrafine powder, because the particle size of the final product is controlled by the classifier. In addition to the cutting particle size, the level of classification efficiency is very important to measure the quality of the air classifier. If the efficiency of the air classifier is high, the quality of the classified products is good, the energy consumption of the grinding operation can also be greatly reduced, and its processing capacity can be significantly improved.
Airflow classifier is a kind of equipment that uses centrifugal force of impeller rotation and drag force generated by airflow to classify materials. The seal between the rotating cage rotor and the stationary shell is an important part of the structure of the vortex air classifier. The failure of the seal is an important reason for the coarsening of the product or the mixing of coarse particles in the finished product.
The sealing method of the air classifier:
(1) Airflow sealing
Ordinary turbo classifiers usually use the high-speed rotation of the classifying wheel to prevent particles from rising to the top of the classifying wheel. Theoretically, the sealing effect can be achieved. Most of the domestic horizontal classifiers also use airflow sealing, but the large particles of the classifying wheel cannot be strictly controlled. Leakage, and due to wear and tear, air consumption gradually increases over time.
(2) Mechanical seal
Mechanical seals can be divided into concave-convex mosaic seals, adjustable gap seals and labyrinth seals.
The main principle of the labyrinth seal is to control the sealing gap to ensure the sealing effect, but because the gap always exists, some coarse or even millimeter particles are directly mixed into the finished product without being sorted by the rotor. Therefore, the mechanical labyrinth seal The sealing effect in the superfine class machine is not good.
The differential pressure air classifier adopts a differential air flow sealing structure, which has the characteristics of high classification accuracy, energy saving, high efficiency and low production cost. It has been widely used in the classification and purification process of quartz, feldspar, mica, kaolin, magnesium oxide, etc. .
Application of non-metallic mineral fillers in plastics industry
Non-metallic mineral fillers generally refer to non-metallic mineral materials that exist in nature and are artificially mined, processed and used to have improved strength and various properties, or to reduce costs, and are added to plastics.
Non-metallic mineral fillers are divided into: oxide, hydroxide, carbonate, (sulfite), silicate, carbon, etc. Oxides mainly include: silicon dioxide, diatomaceous earth, aluminum oxide, titanium dioxide, iron oxide, zinc oxide, magnesium oxide, pumice powder, etc. Hydroxides mainly include: aluminum hydroxide, magnesium hydroxide, basic magnesium carbonate and so on. Carbonates mainly include calcium carbonate, magnesium carbonate, dolomite, basic sodium aluminum carbonate and so on. (Sulfite) mainly includes barium sulfate, ammonium sulfate, calcium sulfate, calcium sulfite and so on. Silicates mainly include talc, clay, mica, asbestos, calcium silicate, montmorillonite, bentonite, glass beads, glass fiber, etc. Carbon mainly includes carbon black, graphite, carbon hollow spheres, carbon fiber, etc. In addition, non-metallic mineral fillers include zinc borate, calcium borate, sodium borate, barium metaborate, and potassium titanate.
The main modification technologies of non-metallic mineral fillers are: surface chemical modification, surface physical coating, plasma surface treatment, phase solvent treatment, mechanical chemical modification, surface graft modification, precipitation reaction modification, in-situ Polymerization technology.
Physical properties and their effects
Specific surface area: The larger the specific surface area, the better the affinity between the filler and the resin, but the more difficult it is to activate the filler surface and the higher the cost.
Hardness: High hardness can improve the wear resistance of the product, but it will wear the processing equipment.
Color: Most plastic production requires Baidu as high as possible.
Optics: Some products can use their light absorption to increase the temperature, such as: agricultural plastic greenhouses.
Electricity: Condensation or crushing on the surface of the particles causes the valence bonds to be broken and charged, causing uneven particle distribution, which should be avoided in actual production.
Chemical properties and effects
Chemical composition: Affects the corrosion resistance, resin structure and qualitative properties of the product. Different types of fillers have different effects on the product, and different fillers are selected according to the required product characteristics.
Thermochemical effect: High molecular polymers are easy to burn, but most inorganic mineral fillers are added to the polymer matrix to reduce the quality of combustibles and delay basic combustion due to their own inconsistency.
Performance requirements for fillers: high chemical stability, good heat resistance, good dispersion and mixing in plastic resin, small absorption of plastic resin, high purity, insoluble in solvents, good acid and alkali resistance, and no moisture absorption.
The role of fillers in plastics
- Calcium carbonate
Calcium carbonate is currently the most widely used powder filler in the plastics industry. Because of its low price, white color, and good processing performance, heavy calcium carbonate can meet the performance requirements of filled plastics, and its dosage is greatly increased.
- Talcum powder
Talcum powder in plastics can improve the rigidity and heat resistance of plastics, and can increase the light transmittance of film scattering rate in plastics, and has a blocking effect on infrared rays with a wavelength of 7-25μm. It has been used in functional films to improve the nighttime of the greenhouse. Heat preservation and promote the growth of crops.
- Kaolin
Kaolin in PVC cable material can significantly improve the electrical insulation of cable sheath; in plastic film, kaolin has better infrared blocking effect than talc, and is used for agricultural film modification; it is also used for polypropylene to make core Agent to improve its mechanical strength.
- Wollastonite
Wollastonite can be used as a plastic reinforcement, can improve the abrasion resistance and dimensional stability of plastic products, and can improve the flame retardant effect of organic flame retardants.
- Mica
The unique flake structure of mica makes it a typical reinforcing filler in plastics, which is mainly used to improve the rigidity, heat resistance and dimensional stability of plastic products. When mica is used in plastic film, its scattered light transmittance can be greatly improved, which is better than other inorganic fillers.
- Aluminum Hydroxide and Magnesium Hydroxide
Aluminum hydroxide and magnesium hydroxide have the three functions of filling, flame retardant and smoke suppression in plastics; they are also the main additives for PVC conveyor belts used in coal mines, and are often filled with epoxy resin and unsaturated polyester products. Adding agent, the amount can reach more than 40%.
The influence of various fillers on plastic properties
Performance | Calcium silicate | Mica | Talc | Graphite | Quartz |
Tensile strength | + | 0 | |||
Compressive strength | + | + | |||
Elastic modulus | ++ | ++ | + | + | |
Impact strength | - | - | - | - | |
Reduce thermal expansion | + | + | + | + | |
Reduce shrinkage | + | + | + | + | + |
Thermal conductivity | + | + | + | + | |
Thermal stability | + | + | + | ||
Conductivity | + | ||||
Electrical insulation | + | ++ | + | ||
Heat resistance | + | + | + | + | |
Chemical resistance | + | + | 0 | + | |
Wear resistance | + | + | + | ||
Extrusion rate | + | ||||
Wear to the machine | 0 | 0 | - | ||
Inexpensiveness | + | + | + | + | ++ |
(++ means high efficiency, + medium efficiency, 0 invalid,-reverse effect)
Performance | Wollastonite | Clay | Calcium carbonate | Carbon black |
Tensile strength | + | |||
Compressive strength | + | |||
Elastic modulus | + | + | + | |
Impact strength | - | - | - | - |
Reduce thermal expansion | + | + | + | + |
Reduce shrinkage | + | + | + | + |
Thermal conductivity | + | + | ||
Thermal stability | + | |||
Conductivity | + | |||
Electrical insulation | + | ++ | ||
Heat resistance | + | + | + | |
Chemical resistance | + | |||
Abrasion resistance | + | |||
Extrusion rate | + | + | ||
Wear on the machine | 0 | 0 | ||
Inexpensiveness | + | + | + |
(++ means high efficiency, + medium efficiency, 0 invalid,-reverse effect)
Plastics with non-metallic minerals added
The role of fillers in plastics
Cost reduction: cheap fillers are added to plastics as fillers to reduce costs. Representative examples include the addition of large amounts of calcium carbonate to polyvinyl chloride and polypropylene.
Improve mechanical properties: Compared with polymer resins, non-metallic minerals have higher hardness and modulus, and its active surface can be combined with polymer chains, so the appropriate addition of non-metallic minerals can effectively improve plastic hardness, modulus, strength and other machinery performance.
Enhanced flame-retardant performance: non-metallic minerals have the advantages of good thermal stability, low toxicity or non-toxicity, no corrosive gas, no play during storage, difficult to precipitate, long-lasting flame retardant effect, etc., and they have abundant raw materials and low prices. It is still a simple and effective method to solve the problems of flame retardancy, low smoke and low toxicity of a large number of flammable engineering plastics.
Enhanced stability: Plastics are used in a variety of environments. Non-metallic mineral fillers can enhance the stability of plastics, such as thermal stability, electrical stability, solvent resistance, and light and thermal aging resistance.
Function: After adding most fillers, plastic products have special functions that they did not have before. This is because the chemical composition of the filler plays an important role. For example, adding graphite can increase the conductivity and wear resistance of the plastic.
The use of mineral fillers in plastic products
Plastic products | Type of filler used | Adding amount (phr) | Effect |
Polypropylene tape | Calcium carbonate | 10~20 | Increase, whiten, improve printability |
Polypropylene strapping | Calcium carbonate | 50~150 | Increase and increase the friction coefficient |
Polyethylene film | Calcium carbonate | 40~50 | Incremental and environmentally friendly |
Polyethylene pipe | Calcium carbonate | 20~40 | Increment |
Polyethylene winding pipe, corrugated pipe | Talc | 20~40 | Increase rigidity |
Polypropylene injection molded products | Calcium carbonate,talcum powder | 40~50 | Replace ABS, reduce costs |
Polyethylene Greenhouse Film | Talc, Kaolin | 5~10 | Improve heat preservation |
Polyethylene garbage bag | Calcium carbonate | 40~50 | Improve incineration |
Polypropylene snack tray | Calcium carbonate | 200 | Reduce costs and improve stability |
Bumper | Talc | 20~30 | Maintain rigidity and improve impact resistance |
Automobile and home appliance parts | Talc | 30~50 | Improve heat resistance |
PVC doors and windows profiled materials | Calcium carbonate | 10 | Improve toughness and forming processability |
PVC pipe | Calcium carbonate | 20~60 | Reduce costs |
PVC foam material | Calcium carbonate | 30~80 | Reduce costs and improve uniformity |
PVC decorative board | Calcium carbonate | 200 | Reduce costs |
Cable sheath material | Calcium carbonate | 10~15 | Reduce costs |
PVC artificial leather | Calcium carbonate | 10~60 | Increment, reduce costs |
Power cable core rope | Calcium carbonate | 180~200 | Reduce costs |
High insulation power cable sheath material | Calcined kaolin | 10~15 | Improve electrical insulation strength |
High gloss polypropylene | Precipitated barium sulfate | 40~50 | Maintain the gloss of the plastic surface |
Halogen-free low-smoke cable sheath material | Aluminum hydroxide, magnesium hydroxide | 150 | Flame retardant, smoke suppression |
Motor fan blades for automobiles, etc. | Mica | 40~50 | Improve heat resistance |
Cases and parts of air conditioners, televisions, etc. | Calcium carbonate, talcum powder | 40~60 | Reduce costs and improve dimensional stability |
The main motivation for using mineral fillers is to reduce the cost of raw materials for plastic products, so price is the primary influencing factor. Coarse particle size fillers tend to be cheaper than fine particle size fillers. Not all plastic products are suitable for the use of mineral fillers. Some are not suitable for use, such as transparent products; some are due to the problems caused by the use of mineral fillers, such as weight gain and poor coloring.
The smaller the particle size of the non-metallic mineral filler, the better the physical and mechanical properties of the filled plastic when used properly. However, within the range allowed by the current technical level and equipment conditions, the particle size is too small, but it is not easy to use, not only the price is high It also affects the fluidity of the molding process and the mechanical properties of the filling material.
More and more attention has been paid to the functionality of non-metallic mineral fillers. Therefore, when developing new varieties of mineral fillers, we must first consider what new functions it can bring to plastic materials.
Article source: China Powder Network
Processing & Application of Powder Quartz
The quartz mined from the mine is processed, and the product with a fineness of less than 120 mesh becomes quartz sand, and the product with a fineness of more than 120 mesh is called quartz powder. It does not require mechanical grinding to obtain high-purity ultra-fine quartz powder, which is called powder quartz, which is different from vein quartz and quartzite.
The physical and chemical properties of powder quartz
- Particle morphology and particle size composition
Powder quartz particle shape: nearly equiaxed hexagonal polyhedron shape. Due to the effect of weathering and leaching, dissolution pits of varying degrees are formed on the surface of the particles. Corrosion passivation makes the particles have the characteristics of high sphericity (the three axes are nearly equal) and low roundness (with edges), which are called "quasi-spherical" particles.
The particle size distribution of powdered quartz is relatively narrow. The main particle size of 400 mesh products is distributed in the range of 5-20μm, the content is greater than 70%, the median particle size is about 14μm, and the particle size is normal.
- Mineral composition and chemical composition
Powder quartz composition: microcrystalline quartz, a very small amount of impurities such as kaolin, mica and plant debris.
The chemical composition of powder quartz: SiO2, Fe2O3, Al2O3, CaO, MgO, K2O, Na2O, TiO2, etc.; spectral analysis results show that powder quartz does not contain Cu, Mn and toxic elements, and other trace elements are close to or below the detection limit.
- Physicochemical properties
Powder Quartz: White, light white powder, Baidu is 50%~75%, brightness is 60%~80%; the dry powder has good dispersibility, no agglomeration, and the hand feels fine and smooth. Density: 2.55~2.65g/cm3, bulk density 1.96g/ml, sedimentation volume 0.6~0.9mg/g, Mohs hardness 7, refractive index 1.544.
The PH value is 6.3, the isoelectric point is PH value of 2~3.7, and the surface is negatively charged in the solution of PH value>3.7; the thermal stability temperature of powdered quartz is 573℃, the melting point is 1730℃, and it has excellent electrical insulation and chemical properties. Inertness and good acid corrosion resistance.
Mineralization Mechanism of Fine Quartz
- Geological characteristics of the deposit
It has the characteristics of both sedimentary deposits and weathered deposits. The ore body is similar in shape to general weathered disabled deposits. The ore body is simple "hat-shaped", layered, layered or belt-like.
- Geological conditions of mineralization
Most of the deposits exist in the Upper Paleozoic Devonian, Carboniferous and Permian strata. The generation of fine quartz ore is related to the regulation of carbonate rock formation, as well as siltstone and high calcareous quartzite. Fine quartz is a weathered crust type deposit, formed by weathered steps of parent rock.
Characterization and modification of powdered quartz
The mineral surface has surface reactive functional groups due to dangling bonds, which are called "surface sites".
Mineral-water interface effect: surface crystal growth and dissolution, surface precipitation and surface reaction. Mineral surface reactions: surface adsorption, oxidation-reduction and ex-situ catalytic reactions. These surface reactions are mainly determined by the reactivity of the mineral surface and various properties of the aqueous medium. The surface reactivity of minerals is usually related to surface properties such as mineral composition, surface structure and micro-topography.
Modification of powdered quartz: change the compatibility of the filler with organic polymers, reduce the viscosity of the filler-polymer mixed system, increase the filler, improve the infiltration and dispersibility of the filler in the polymer, eliminate chemical and mechanical damage points, improve the product Physical and mechanical properties.
Modification method of powdered quartz: dry method and wet method. The wet process is complex, high in cost, and less industrialized. Modification process: powdered quartz → preheating and stirring → (modification aid preparation →) modification aid → heating and drying → (coupling agent preparation →) silane coupling agent → surface modification → screening and degranulation → modification Pink quartz
Processing and Application of Powder Quartz
Natural powdered quartz generally has high purity and few impurities, and can be used without grinding. It is often used as a natural powdered siliceous material and is widely used in electrical insulation, waterproof and corrosion resistant, precision investment casting and new building materials. Powdered quartz is also used as the most common inorganic filler for epoxy resins in rubber, plastics and paint extender pigments.
Powdered quartz can be used in abrasive industry, glass industry, ceramic industry, paint manufacturing industry, rubber and plastic industry, coating industry, refractory materials, microporous calcium silicate insulation materials, etc.
In the abrasive industry, natural silica abrasive is one of the indispensable abrasive materials in the machining of precision parts in the machinery industry. It is widely used for sanding and matting and direct grinding of various high-finish mechanical parts.
In the glass industry, ordinary flat glass requires a SiO2 content of more than 96%. The SiO2 content of powdered quartz after grading desliming can reach 98%. It can be used for the production of flat glass only by sieving and removing the fine-grained powder.
In the ceramic industry, paint and pharmaceutical industry, rubber and plastic industry, powdered quartz products can be directly used after beneficiation processing and classification. The powder quartz used for ordinary ceramics is required to be above 98.5%, and the powder quartz after elutriation can almost meet these requirements. Some products using powdered quartz as raw materials are superior in performance to products made using veined quartz as raw materials. It can improve the strength and insulation of ceramics, as well as the durability and smoothness of paint. It can also make synthetic rubber and plastic products have high acid and alkali resistance.
There are also applications in the field of coatings, such as the use of modified powdered quartz in anti-radon coatings to replace heavy calcium used in traditional anti-radon coatings, reducing coating production costs and increasing the industrial added value of powdered quartz.

Powdered quartz is mainly used in refractory materials to produce high-density silica bricks and regulated refractory mud. The raw ore of powdered quartz has the characteristics of wide particle size distribution and low silicon content and low alumina. It is an ideal raw material for high-density silica bricks. The softening point is as high as 170°C, which is suitable for glass furnaces with higher melting temperatures. The siliceous refractory clay prepared with powdered quartz has high thermal strength, can significantly improve the masonry performance of silica bricks, prolong the service life of the furnace body, and reduce the masonry cost.
Precision casting is also called investment casting. Powdered quartz is mainly used as a filler for investment coatings. Investment coatings are prepared from sodium silicate, surfactants, water and powdered quartz. Powder quartz is mainly used as refractory material in investment coatings and improves the gloss of the casting surface. Therefore, the quality of powdered quartz directly affects the quality of the surface of the casting and the yield of casting.
The microporous calcium silicate insulation material is mainly synthesized by the hydrothermal gel reaction of siliceous raw materials and lime slurry. It has light bulk density, low thermal conductivity, high operating temperature, low heat loss... It is widely used in electric power, petroleum, chemical soil, light industry, construction and metallurgy and other fields. Commonly used raw materials have low SiO2 content, poor thermal insulation effect, and high cost of vein quartz. Powdered quartz is an ideal raw material for the synthesis of microporous calcium silicate.
Article source: China Powder Network
What factors will affect the working efficiency of the jet mill
Jet mill is a device that uses high-speed airflow for grinding. After compressed air is filtered and dried, it is jetted into the grinding chamber at high speed through Laval nozzles. At the intersection of multiple high-pressure airflows, the materials are repeatedly collided, rubbed, and sheared to be crushed. .
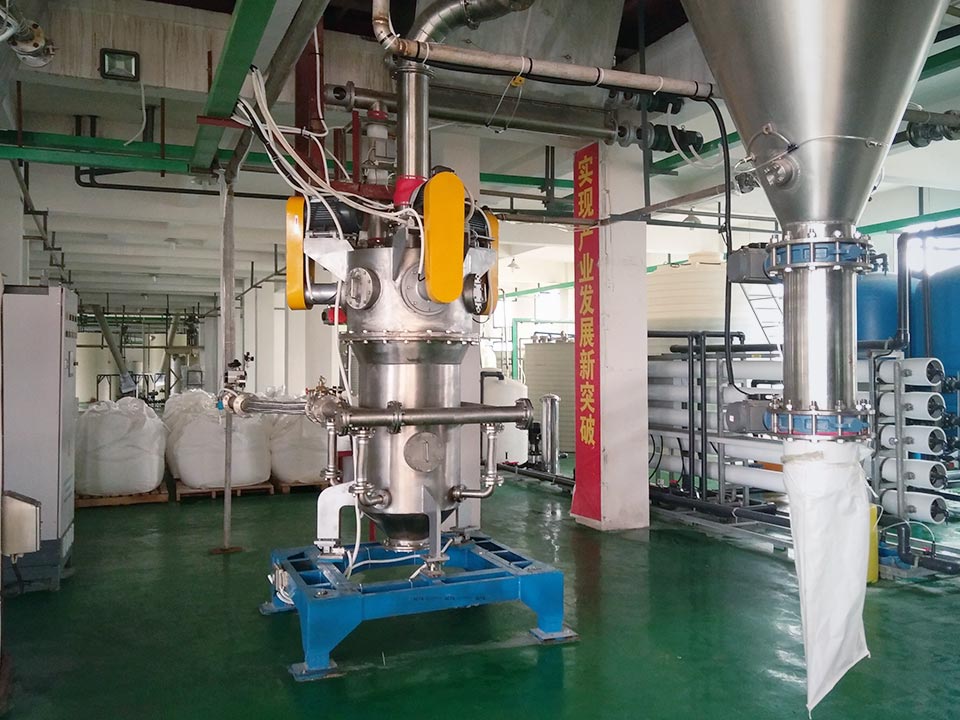
There are several factors that affect the working efficiency of the jet mill.
1. Material characteristics. Generally speaking, the jet mill can be adapted to the crushing of all brittle materials. However, due to the different properties of the materials, their crushing performance is also different. Due to the difference in the strength, density, hardness, viscosity, shape and electrical properties of various materials, the difference in grinding results is inevitably caused, and the strength of the material is an important factor. In addition, because the moisture content of water or oil in some materials or air sources is too high, the properties of the abrasive material (such as the increase in toughness and viscosity) will affect the fineness of the grinding.
2. Processing volume, the same material has different grinding fineness due to different processing volume. Generally speaking, the processing capacity is directly proportional to the particle size of the product. However, if the processing volume is too small, the chance of collisions between particles will be reduced, thereby affecting the fineness.
3. The influence of back pressure, the back pressure is the average pressure of the gas in the crushing chamber. Since the spray speed of the crushing nozzle is mainly determined by the difference between the nozzle inlet pressure and the outlet pressure, the greater the pressure difference, the greater the flow rate. Therefore, the increase in back pressure is not conducive to polishing. In production, the increase in the resistance of the capture system will increase the back pressure of the jet mill and affect the grinding effect of the powder. Therefore, be sure to check the resistance of the capture system.
Ultra-fine grinding of kaolin
The main mineral composition of kaolin is 90% kaolin + 10% halloysite, quartz, jellyfish stone, etc., commonly known as "china clay". The world's kaolin resources are rich and widely distributed. At present, the world has identified about 20.9 billion tons of kaolin resources. In the world, the Americas are the main producing areas of kaolin, and kaolin production accounts for about 35% of the world's total output; Europe's kaolin production has long been ranked second in the world, accounting for about 30% of the world's total output.
Kaolin is divided into hard kaolin, light kaolin and sandy kaolin.
Hard kaolin: hard (Mohs hardness 3~4), no plasticity, plasticity only after crushing and fine grinding. This kind of kaolin is dark gray, brown, etc. due to its high-quality impurities.
Lightweight kaolin: soft, generally strong plasticity, sand content <50%.
Sandy kaolin: soft, general plasticity, strong plasticity after sand removal, sand content ≥50%.
Kaolin is widely used and can be used in ceramic industry, paper industry, rubber industry, enamel industry, refractory material industry, environmental protection and chemical industry, etc.
Ceramic industry: mainly used for daily-use ceramics, architectural ceramics, sanitary ceramics, special ceramics and arts and crafts ceramics.
Paper industry: used as fillers and coatings for papermaking.
Rubber industry: used as a filling and reinforcing agent for rubber products.
Enamel industry: Kaolin with high whiteness, fine particle size and good suspension performance is used as silicate glass coating for enamel products.
Refractory industry: multi-clinker refractories, semi-acid refractories, etc.
Environmental protection and chemical industry: production of polyaluminum, treatment of industrial domestic water, production of alum, aluminum chloride and other chemical agents.
The whiteness of kaolin is one of the important indicators that determine its application value. The dyeing impurities in kaolin are mainly iron, titanium minerals and organic matter. Iron and titanium mostly exist in the form of hematite, goethite, pyrite, siderite and other minerals, and their distribution in kaolin is also very complicated, and most of the crystalline ones are mixed with fine particles. Since iron-containing minerals will become Fe2O3 when calcined at high temperatures, the raw materials will turn yellow or brick red. Therefore, measures to remove iron must be taken before or during calcination to increase the whiteness of the product to 92% or higher.
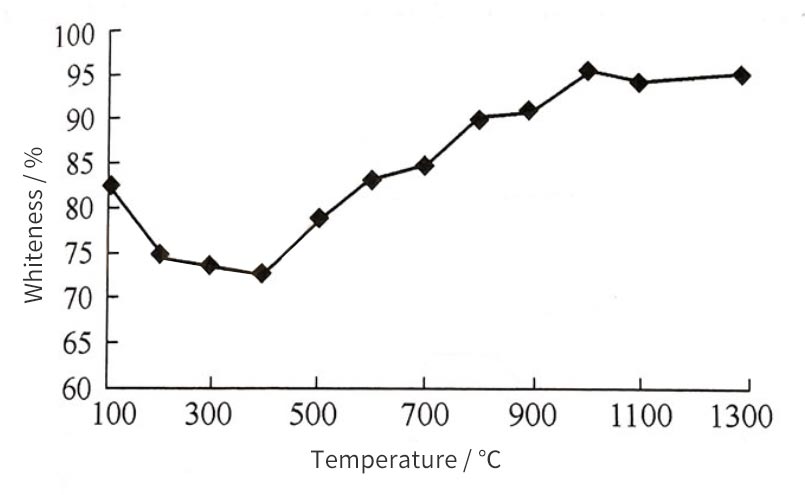
Ultra-fine grinding process of kaolin
In the deep processing of kaolin, in addition to whiteness, purity and other indicators, in order to meet the technical requirements of coated paper, coated paper, cardboard, as well as high-end paints and coatings, plastic box rubber products, etc., the particle size and fineness of kaolin products are very important. index of. At present, the ultra-fine technology with many high-end "double 90" products is basically becoming mature, and its processes are mainly divided into two types: dry method and wet method.
- Dry grinding process
Dry grinding is mostly used for ultra-fine grinding of hard kaolin or kaolin, especially for directly processing kaolin into ultra-fine powder that can meet user requirements. At present, the product fineness that can be achieved by dry production is generally D90≤10μm, that is, the final product is about 1250 mesh.
Dry ultra-fine grinding equipment is mostly jet mill, high-speed mechanical impact mill, vibration mill, etc.
In order to produce high-grade kaolin products, a two-stage ultra-fine grinding process can be used. The first stage uses an impact crusher, the second stage uses a jet crusher, plus certain grading equipment to obtain a product with a size of -2μm accounting for 80% to 90%. . In order to control the product size, especially the largest particle content, it is often necessary to configure fine grading equipment.
- Wet superfine grinding process
The ultra-fine grinding method must be used to produce paint-grade high-grade kaolin products with D90≤2μm during wet ultra-fine grinding.
Before the wet superfine grinding, the kaolin is pulped by a masher, and at the same time, it can be purified, whitened, and classified in the process, and then superfine grinding is carried out with equipment such as a peeling machine and a stirring mill. In order to make the product particle size D90≤2μm, multiple peeling machines can be used for multi-stage peeling and ultra-fine grinding during the ultra-fine grinding process.
Kaolin has flaky crystals, and ultra-flaky kaolin has excellent performance when used as a filler. Therefore, the wet ultra-fine pulverization of kaolin is also called peeling, which means that the thicker laminated kaolin is peeled off into thinner flakes, while maintaining Its original crystal characteristics. The peeling methods include wet grinding, squeezing and chemical soaking.
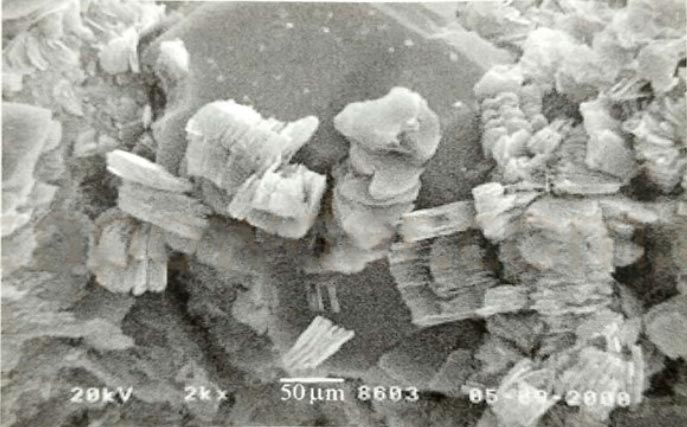
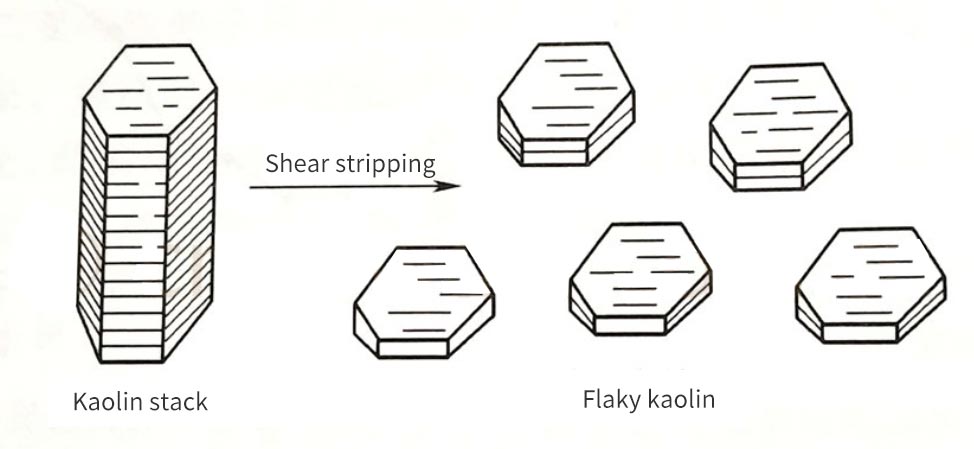
Article source: China Powder Network
How to extend the service life of jet mill
After working for a long time, how to update and maintain the jet mill to make its lifespan longer, bring more benefits to manufacturers and save energy.
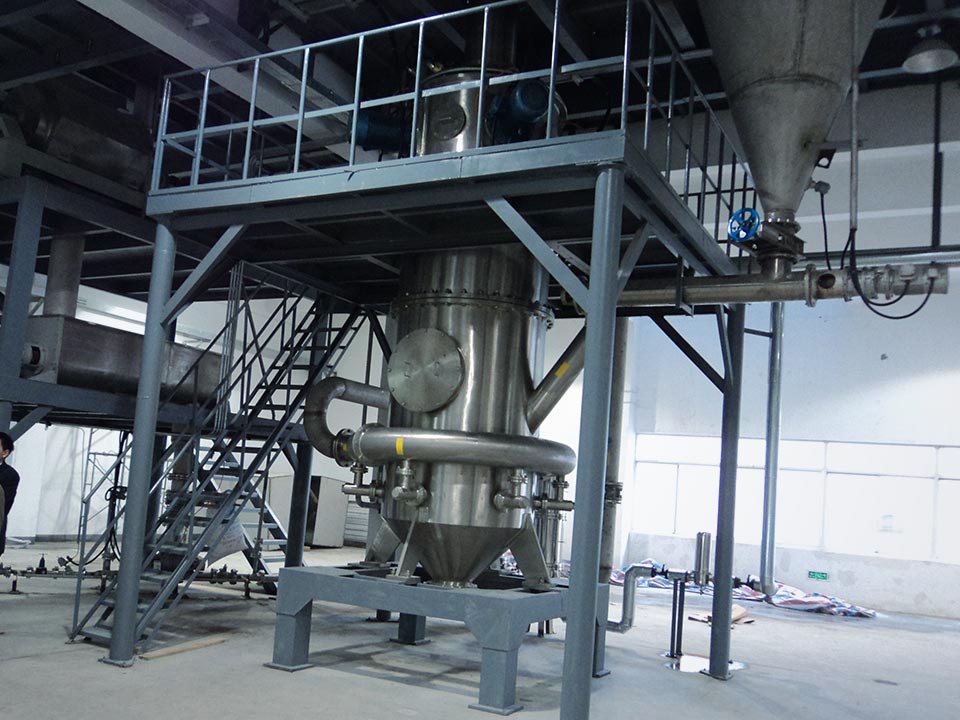
(1) The jet mill will accumulate a lot of dust under long-term work. How to clean it at this time? When cleaning it, the motor and bearings cannot be wetted. The all-ceramic grinder adopts advanced grinding technology and manufacturing level. It is a high-efficiency equipment for grinding hard and abrasive materials. It is especially suitable for grinding highways, railways, airport runways and other engineering buildings. Highways, railways, airport runways and other engineering stones are mostly hard rock such as basalt, with specifications of 3-7 cm or 2-8 cm, and the hardness of the crushed materials is relatively large. General grinders are not only low in output but also easy to wear. .
(2) When replacing parts or performing updates and maintenance, work must be performed under power-off conditions, and prominent warning signs should be hung up.
(3) Lubricate the machine in time to make it more efficient.
(4) Lubricating oil must be added after the working time of the general classification part is 1500 hours.
(5) When the open-air work is completed, the interior must be cleaned and cleaned. Cover it with fireproof cloth and rainproof cloth to prevent internal machinery from rusting. It must be fireproof and waterproof with multiple precautions.
(6) If there is a sudden stop of work, the power must be turned off first, and we are performing maintenance after the power is off. When the machine is running, the body should be locked and it is strictly forbidden to open it.
(7) When the machine is working normally, it must be equipped with belts for installation safety protection to prevent personal safety.
Some of the above methods are measures that can extend the life of the jet mill. The all-ceramic crusher is a new type of fine grinding and coarse grinding product developed by optimizing the main technical parameters. It has the characteristics of large grinding ratio, low energy consumption, stable operation, simple structure, convenient operation and maintenance, etc. It is a truly multi-purpose, A new type of high-efficiency, low-cost grinding equipment.
Application of diatomite
Diatomaceous earth is a kind of biochemical sediment, mainly formed by the accumulation of fossil bone remains of single-celled plant algae in ancient geological period, and is a non-renewable natural resource. Its main mineral composition is opal and its variants, and its chemical composition is mainly SiO2, and contains a small amount of Al2O3, Fe2O3, CaO, Na2O, MgO, etc.
Diatomaceous earth is commonly known as mountain powder, fossil powder or radiolarian powder. It is an important high-efficiency non-metallic mineral. It has many advantages such as large porosity and strong adsorption. It can be used in building materials, light industry, chemical industry, petroleum, food grade and environmental protection field.
Pure diatomaceous earth is generally in the form of white soil. When it contains impurities, it is often polluted by iron oxides or organic matter and becomes gray, yellow, green, and black. Most diatomaceous earth is light, porous and easily broken, but the hardness of the diatomaceous earth bone particles is relatively large. The density of diatomaceous earth is very small, the average bulk density: 0.66g/cm3, thermal stability: After the original soil is calcined at 900℃ for 2h, the regularly arranged pore structure of the diatom shell wall remains intact. When it is calcined at 1200℃ for 2h, then The arrangement of diatom pores will be destroyed.
The particle structure of diatomaceous earth is closely related to diatoms. The individual diatoms are small, generally 1~100μm. The mineral composition of diatom remains is amorphous SiO2, which has good chemical stability and is thermal, acoustic and electrical of poor conductors.
The chemical composition of diatomaceous earth is mainly silicate, and the level of silica content is an important indicator to measure the quality of diatomaceous earth. It can be divided into high-grade diatomaceous earth and inferior diatomaceous earth.
Diatomaceous earth is a solid acid, which is weakly acidic. In addition to being soluble in hydrofluoric acid, it is insoluble in other acids and can react with weak bases. Its surface adsorption properties are related to its surface structure. The surface of diatomaceous earth is covered by a large number of silyl hydroxyl groups, and there are hydrogen bonds. OH groups are also distributed on the inner surface of the pores of the diatomaceous earth.
Diatomite is rich in resources and widely distributed around the world, mainly distributed in 122 countries and regions such as the United States, China, Argentina, Peru, Denmark, and Japan. However, the resource grade and economic value are high, and the mineral deposits that can be directly developed and utilized are not many. At present, dozens of countries and regions produce diatomite products with an annual output of hundreds of tons. The largest output is the United States, followed by Russia, France and Germany.
Application of diatomite
- Filter aid
Filter aid is a granular material with uniform particles, hard properties and small compressibility. Its function is to filter and separate small particles and prevent colloidal particles from clogging the medium. The most widespread use of diatomaceous earth is as a filter aid for separating suspended solids in liquids. The reason why diatomaceous earth is suitable as a filter aid is that it has poor solubility, suitable particle size distribution and porous structure.
- Application in building materials industry
(1) Application of diatomite in interior wall coatings
The diatom mud made of diatomite as a raw material is used in interior decoration coatings, especially interior wall coatings, and has very good effects on the purification of indoor air and the adjustment of temperature and humidity.
(2) Application of diatomite in environmental protection wall materials
Due to the unique physical structure of diatomite, the diatom mud can fully absorb the formaldehyde and benzene present in the air, and it also has a great promotion effect on indoor air purification, which is very helpful to keep the indoor air fresh.
(3) Application of diatomite in concrete
An obvious application of diatomite in the building materials industry is concrete. Determined by the nature of diatomaceous earth, the surface of diatomaceous earth is rough, and it has strong advantages in high temperature resistance and corrosion resistance. When used with asphalt materials, it can effectively improve the quality of concrete.
(4) Application of diatomite in lightweight wall materials
Diatomite is used in lightweight wall materials and has great advantages in plasticity and sintering molding. After processing, the hardness is also greatly improved. This is due to the fact that there are many pores on the surface of diatomaceous earth, which can allow other materials to merge into the pores. After processing, the wall can be insulated and the weight is greatly reduced.
- Catalyst carrier
Diatomaceous earth is inert to most chemical reactions and resistant to high temperatures, so it can be used as an ideal catalyst carrier. Generally used as a catalyst for chemical reactions such as oxidation, hydrogenation, dehydrogenation, hydration, and reduction. For example, the nickel catalyst in the hydrogenation process, the vanadium catalyst in the preparation of sulfuric acid, the phosphorus catalyst used in petroleum refining, and the catalyst for automobile exhaust gas treatment can all be supported by diatomaceous earth.
- Adsorbent
Diatomaceous earth adsorbent is mainly used for the decolorization and refining of mineral oil, animal and vegetable oils, adsorbing and removing asphaltenes, neutral collagen, sulfide olefins, naphthenic acid, minerals, carotene, lutein, chlorophyll, etc.
Article source: China Powder Network
The difference between open-circuit jet mill and closed-circuit jet mill
Jet mill is a kind of micron level ultra-fine grinding equipment, which is more common in various powder industries. The jet mill has two different structures, divided into open-circuit and closed-circuit. The open circuit system usually refers to the use of air as a medium to crush, filter and discharge after crushing. The closed-circuit system refers to the use of inert gas as the medium. The materials in the system are under the protection of inert gas during the entire process of feeding, crushing, grading, conveying, separating and packaging. After dust removal and filtration, the inert gas is returned to the front-end system for recycling.
1. Open-circuit jet mill
Jet mill (fluidized bed jet mill) is the compressed air accelerated by Laval nozzle into supersonic air flow and then injected into the crushing zone to make the material fluidized (air flow expands into fluidized bed suspension boiling and collides with each other), so Each particle has the same state of motion. In the crushing zone, the accelerated particles collide and crush at the intersection of the nozzles. The crushed materials are transported to the grading area by the ascending airflow, and the fine powder that meets the particle size requirements is screened out by the grading wheel, and the coarse powder that does not meet the particle size requirements is returned to the crushing area to continue pulverization. The qualified fine powder enters the high-efficiency cyclone separator along with the air flow and is collected, and the dust-containing gas is filtered and purified by the dust collector and then discharged.
2. Closed-circuit jet mill
The closed-circuit jet mill generally refers to the air jet mill based on the air outlet of the pulse dust collector connected with the air inlet of the air compressor that provides the power source of the system to form a closed system to make the smashing medium of the entire pulverization process ( Air or inert gases such as nitrogen, argon, helium, carbon dioxide, etc.) circulate in a closed system.
The closed-circuit jet mill is a closed-circuit jet pulverization system developed for the crushing requirements of special materials such as flammable, explosive, easy to oxidize, and volatile. It is protected by inert gas circulation. The working process is that the cooled inert gas is accelerated by the Laval nozzle into a supersonic airflow and sprayed into the central crushing area of the pulverizer. The sonic airflow brings the animal material to collide with each other in the crushing area to achieve the goal of crushing. The crushed material enters the classification area with the updraft, and the powder material that meets the particle size requirements is sorted by the classification wheel in the classification area. The particle size of the powder is sorted by adjusting the speed of the grading wheel. The sorted products are discharged from the centrifugal separator along with the airflow or collected after being filtered by the dust collector. The unqualified ones continue to return to the crushing area for two Smashed. The filtered inert gas is compressed and recycled by the compressor system, and the whole process is automated.
The open-circuit jet mill can be used for the processing of most common powder materials, and the closed-circuit jet mill is mainly used for flammable, explosive, and oxidizable raw materials. The user can choose according to the raw materials and processing requirements.
Performance of Titanium Dioxide & Its Function and Application in Coatings
Titanium dioxide pigments are divided into two types: anatase type and rutile type. According to international practice, they are called R type and A type respectively. The rutile type and anatase type without post-treatment are called RI type and AI type respectively; the rutile type and anatase type after the post-treatment are called R2, R3 and A2 type respectively. At present, most of the rutile titanium dioxides on the market belong to R2 and R3 types, of which R2 type accounts for more than 70% of sales. R2 and R3 account for 77% and 22% of rutile titanium dioxide for coatings, respectively.
Performance and use of pigment grade titanium dioxide
Pigment-based titanium dioxide has high refractive index, strong achromatic power, large hiding power, good dispersibility, good whiteness, non-toxic, stable physical and chemical properties, and excellent optical and electrical properties, so it has a wide range of uses , Paint, plastic, paper, chemical fiber, ink, rubber, cosmetics, etc. all use pigment-grade titanium dioxide. Among them, the largest amount is paint, accounting for about 57%. In particular, rutile titanium dioxide is mostly consumed by the coating industry. With the rapid rise of China's automobile industry, construction industry and water-based coatings, the coating industry not only needs more titanium dioxide in quantity, but also has higher quality requirements and more varieties.
The refractive index of rutile titanium dioxide is 2.76, and the refractive index of anatase titanium dioxide is 2.55. The hiding power is determined by the difference between the refractive index of the pigment and the refractive index of the medium, and their relative values can be calculated according to the formula. The reflection coefficient of rutile titanium dioxide is 25% to 30% higher than that of anatase titanium dioxide, which means that if it produces the same hiding power as anatase titanium dioxide, the amount of rutile titanium dioxide can be reduced by 25% to 30%. In addition, rutile titanium dioxide has a compact structure, relatively stable, low photochemical activity, resistance to ultraviolet light, is not easy to pulverize outdoors, and has better weather resistance and gloss than anatase titanium dioxide. Therefore, it is widely used in various outdoor coatings with high weather resistance for high-grade ships, bridges, automobiles, buildings, etc., which accounts for about 70% of the coatings. Anatase titanium dioxide is easy to pulverize and yellow, so it is generally only used For indoor coatings or primers, the amount only accounts for 30% of the titanium dioxide used in coatings.
The role of pigment grade titanium dioxide in coatings
Coatings are viscous suspensions composed of base materials, pigments, fillers, solvents and additives. It is coated on the surface of the object to form a tough coating film, which plays a role of decoration and protection on the object.
Regardless of solvent-based or water-based coatings, if titanium dioxide is used, its role is not only to cover and decorate, but also to improve the physical and chemical properties of the coating, enhance chemical stability, and even improve hiding power, color reducing power, and corrosion resistance., Light resistance, weather resistance, enhance the mechanical strength and adhesion of the paint film, prevent cracks, prevent the penetration of ultraviolet rays and moisture, thereby delaying aging and extending the life of the paint film. At the same time, it can save materials and increase varieties.
Regardless of solvent-based or water-based coatings, if titanium dioxide is used, its role is not only to cover and decorate, but also to improve the physical and chemical properties of the coating, enhance chemical stability, and even improve hiding power, color reduction power, and corrosion resistance. , Light resistance, weather resistance, enhance the mechanical strength and adhesion of the paint film, prevent cracks, prevent the penetration of ultraviolet rays and moisture, thereby delaying aging and extending the life of the paint film. At the same time, it can save materials and increase varieties.
Among the pigments, white pigments are the most widely used. Both white paints and light-colored paints use it. Therefore, the amount of white pigments used in paint production is much more than other pigments. The white pigments commonly used in coatings include zinc white, lithopone, titanium white and so on. Because some synthetic resin coatings have a high degree of polymerization, if zinc white is added, the zinc white will have a tendency to thicken due to its alkalinity and anti-acid effect with the free fat in the coating; if zinc white is added, the weather resistance will be poor. But the use of titanium dioxide can improve the above shortcomings. Because the titanium dioxide particles are small and uniform, and the photochemical stability is high, in terms of hiding power, rutile titanium dioxide is 7 times that of zinc white and 5.56 times that of lithopone, and anatase titanium dioxide is 5.57 times that of zinc white. Lithopone is 4.3 times; in terms of decoloring power, rutile titanium dioxide is 8.3 times that of zinc white and 6.25 times that of lithopone. Anatase type titanium dioxide is 6.4 times that of zinc white and 4.8 times that of lithopone. Times. In terms of use effect, 1t of titanium dioxide is at least equivalent to 4t of lithopone; in terms of service life (referring to outdoor chalking resistance), the coating with titanium white as a pigment is 3 times higher than that with lithopone as a pigment. Therefore, the use of titanium dioxide can greatly reduce the amount of pigments in the entire coating, and the coatings made are bright in color, not easy to yellow, light resistance, heat resistance, abrasion resistance, weather resistance, alkali resistance, sulfur resistance, and dilute acid resistance. It is precisely because titanium white has superior performance than zinc white and lithopone, it has become the best white pigment indispensable in paint production. The amount of titanium dioxide accounts for more than 90% of the total amount of pigments used in coatings, and more than 95% of the total amount of white pigments used in coatings. It accounts for 10% to 25% of the cost of coating raw materials.
Article source: China Powder Network
Ultra-fine grinder helps the development of lithium battery materials
The ultra-fine grinder has a uniquely designed grading chamber and a grading wheel with frequency conversion speed regulation. It does not need to be equipped with a screen and can classify the product size at a low speed. The circulating feed structure not only strictly limits the "large particles", but also avoids excessive crushing, so the product has a narrow particle size distribution. The classification wheel is used for classification, which avoids the difficulty of passing the powder with more than 150 mesh.
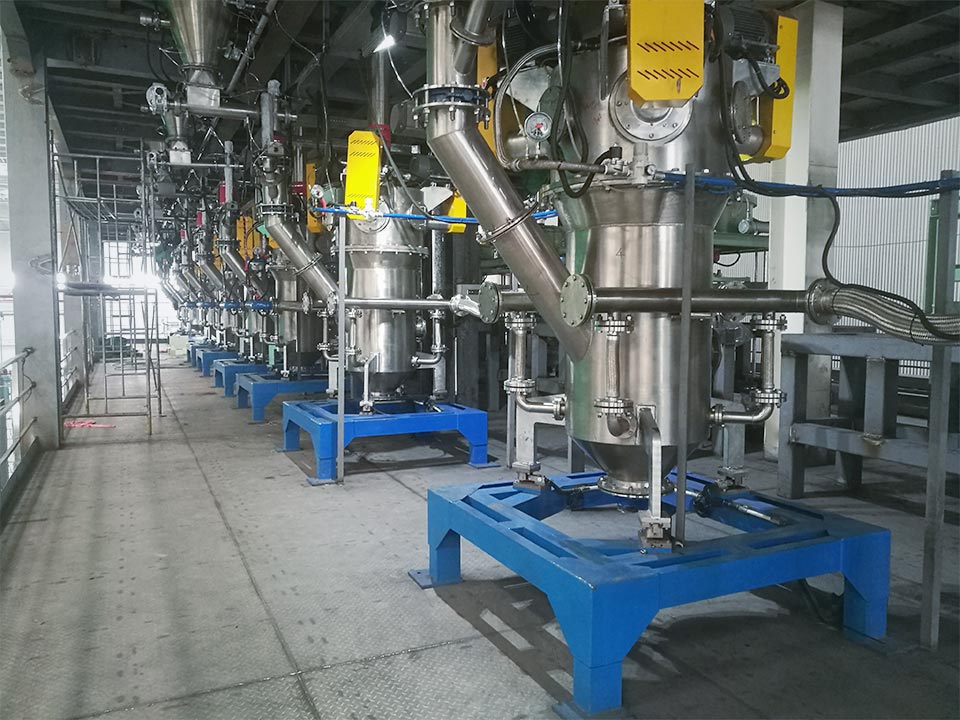
The main wear parts of the ultra-fine grinder: flat teeth, round teeth, large and small grinding teeth. The flat teeth and round teeth are made of stainless steel and have a good dynamic balance. If they are severely worn, they should be replaced. The size of the self-made metal processing should be specified, and the weight difference of each piece shall not exceed 1g to avoid vibration damage to the bearing and the machine.
At present, ultra-fine grinders have been used in batches for the cathode materials of lithium batteries, mainly including lithium cobalt oxide, lithium nickel oxide, lithium manganate, lithium nickel cobalt manganate (ternary material) and lithium iron phosphate. The crushing of the cathode material is a very critical process. Currently, commonly used equipment includes jet mills, mechanical mills, and sand mills.
As the capacity of the lithium-ion battery increases, the internal energy stored increases, and the internal temperature will increase. In severe cases, a short circuit may occur, thereby damaging the battery. Coating high-purity ultra-fine alumina on the surface of PP, PE or multilayer composite diaphragm can improve the safety of lithium-ion batteries.
What is the working principle of the ultra-fine grinder? The high-speed airflow generated by the air source system enters the pulverizing system, causing the material to rotate at a high speed, and the material collides with the material to achieve the purpose of ultra-fine pulverization. When materials enter the grading system, only materials that meet the particle size requirements will be collected, and those that do not meet the particle size requirements will be sent back to the crushing chamber to continue crushing. Repeat this process until the material meets the standard. The ultra-fine grinder can be used for the pulverization of chemical raw materials and non-metallic minerals.