Ultrafine grinding of dry and hard solid materials
In the modern industry, there are many follow-up products that require ultra-fine grinding of materials, such as black tea, ultra-fine grinding of tea leaves, such as ultra-fine grinding of rice husk powder, used to make special bags; ultra-fine grinding of silicon carbide, Used in various industries, etc., etc., are inseparable from the ultra-fine grinder.
The modern ultrafine grinder can set different types of pulverization for different materials, and can also customize different sizes of ultrafine grinder according to the size of the output. This modern ultrafine grinder has large output, low noise, convenient cleaning, sturdiness and durability. It is in line with the current trend of ultrafine grinding of materials and has become the new darling of current fashion.
The ultra-fine grinder is especially suitable for ultra-fine grnding of dry materials and hard materials. The grinding process is finer and the output is larger. The hard carbon powder structure of diamond can be ultra-finely pulverized, and the requirements of modern ultra-fine grinder for materials are as dry as possible.
The ultra-fine grinder is completely carried out in a closed environment when performing ultra-fine grinding, will not produce dust spills, and protect the working environment of workers. It is a very environmentally friendly mechanical equipment. According to the different grinding media, the ultrafine grinder is divided into jet pulverizer and mechanical grinder. The jet mill can be filled with air or special gas for ultra-fine grinding to ensure the integrity of the material. The mechanical crusher can be divided into many types, small rod crushing, etc. The specific principle is to perform ultrafine crushing through the collision of materials and equipment. However, no matter what kind of ultrafine grinder, it is very environmentally friendly in the process of grinding materials. The output can range from one catty to more than 100 catties per hour, and the fineness varies from a few hundred meshes to thousands of meshes.
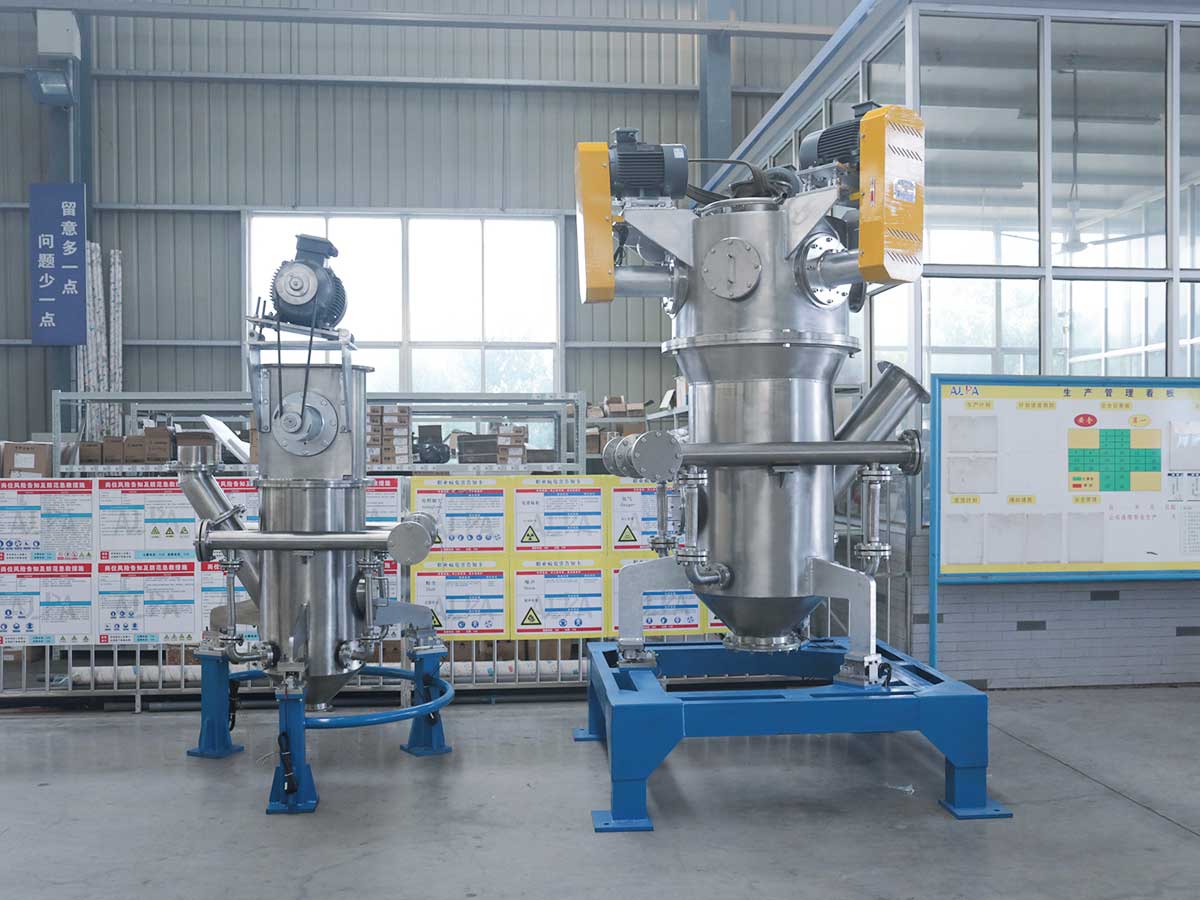
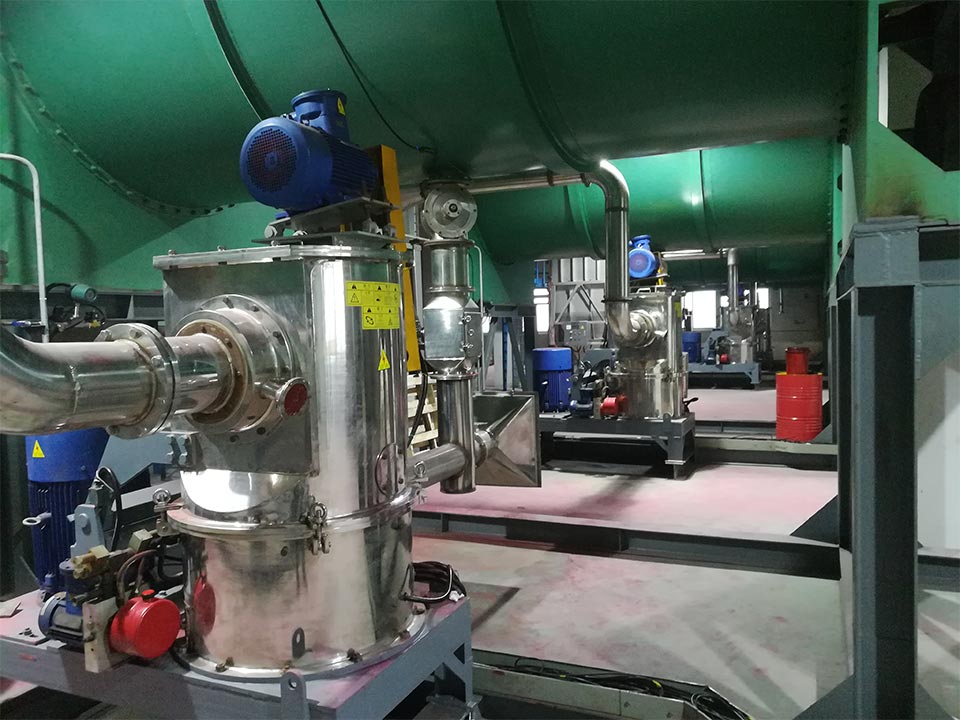
With the development of the times, ultra-fine grinders are used in chemical, mining, abrasives, refractory materials, battery materials, metallurgy, building materials, pharmaceuticals, ceramics, food, feed, new materials and other industries and the ultra-fine grinding of various dry powder materials. Dispersion and other aspects have been widely used. It is suitable for dry grinding of various materials with Mohs hardness below 9 and is especially suitable for the grinding of materials with high hardness, high purity and high added value. The crushed material has good particle shape and narrow particle size distribution.
Features and application of silicon powder
Silicon micropowder is made of natural quartz (SiO2) or fused quartz (amorphous SiO2 after high temperature melting and cooling of natural quartz) after crushing, ball milling (or vibration, jet milling), flotation, pickling purification, high-purity water treatment, etc. The micro powder processed by this technology. Silica powder is a non-toxic, odorless, non-polluting inorganic non-metallic material.
Physical and chemical properties
1. The appearance of silica powder is gray or off-white powder, and its refractoriness is >1600°C. Bulk density: 200~250 kg/m3.
2. The fineness of silica fume: more than 80% of the silica fume has a fineness of less than 1 micron, the average particle size is 0.1-0.3 microns, and the specific surface area is 20-28m2/g. Its fineness and specific surface area are about 80-100 times that of cement and 50-70 times that of fly ash. Common specifications for quartz powder are 400 mesh, 800 mesh, 1000 mesh, 1500 mesh and 2000 mesh.
3. Particle morphology and mineral phase structure: During the formation process of silica fume, due to the effect of surface tension during the phase transition, amorphous spherical particles of amorphous phase are formed, and the surface is relatively smooth, and some have multiple circles. An agglomerate of spherical particles sticking together. It is a kind of volcanic ash material with large specific surface area and high activity. For materials mixed with silica fume, tiny spheres can play a lubricating effect.
Silica powder can fill the pores between cement particles, and at the same time form a gel with the hydration product, and react with the alkaline material magnesium oxide to form a gel. In cement-based concrete, mortar and refractory castables, mixing a proper amount of silica fume can play the following role:
1. Significantly improve the compressive, flexural, impermeable, anti-corrosion, impact and wear resistance properties.
2. It has the functions of retaining water, preventing segregation and bleeding, and greatly reducing the resistance of concrete pumping.
3. Significantly prolong the service life of concrete. Especially in harsh environments such as chloride pollution erosion, sulfate erosion, and high humidity, the durability of concrete can be doubled or even several times higher.
4. Significantly reduce the floor ash of sprayed concrete and castables, and increase the thickness of a single sprayed layer.
5. It is a necessary component of high-strength concrete, and C150 concrete has been applied in engineering.
6. It has about 5 times the effect of cement. It can reduce costs and improve durability when used in ordinary concrete and low-cement castables.
7. Effectively prevent the occurrence of concrete alkali aggregate reaction.
8. Improve the compactness of castable refractories. When coexisting with Al2O3, it is easier to form mullite phase, which increases its high-temperature strength and thermal shock resistance.
Application field
1. Used in mortar and concrete: high-rise buildings, seaports, reservoirs and dams, water conservancy, culvert gates, railways, highways, bridges, subways, tunnels, airport runways, concrete pavements and coal mine tunnels, etc.
2. In the material industry:
- High-grade, high-performance, low-cement refractory castables and prefabricated parts have a service life three times that of ordinary castables. The refractoriness is increased by about 100°C, and the high-temperature strength and thermal shock resistance are significantly improved. Has been widely used in: coke oven, ironmaking, steelmaking, steel rolling, non-ferrous metals, glass, ceramics and power generation industries.
- Large iron trenches and ladle materials, air-permeable bricks, smear repair materials, etc.
- Construction application of self-flowing refractory casting material and dry-wet spraying.
- Oxide-bonded silicon carbide products (ceramic kiln furniture, flame screens, etc.).
- High temperature type calcium silicate light-weight thermal insulation material.
- The corundum mullite push plate is used for the electric porcelain kiln.
- High temperature wear-resistant materials and products.
- Corundum and ceramic products.
- Sialon combined products.
At present, in addition to being widely used in castable refractories, it has also been widely used in fused and sintered refractories.
3. New wall materials and facing materials:
- Polymer mortar, thermal insulation mortar and interface agent for wall insulation.
- Cement-based polymer waterproof material.
- Lightweight aggregate thermal insulation and energy-saving concrete and products.
- Putty powder processing for interior and exterior wall construction.
4. Other uses:
- Silicate brick material.
- Production of water glass.
- Used as a reinforcing material for organic compounds. Because its composition is similar to that of white carbon black produced by gas phase method. It can be used as a filling and reinforcing material in polymer materials such as rubber, resin, paint, paint, unsaturated polyester, etc.
- Used as an anti-caking agent in the fertilizer industry.
Article source: China Powder Network
Chinese medicine ultrafine pulverization technology
Regarding the ultrafine grinding of traditional Chinese medicine, researchers have given different names and concepts from different research perspectives, such as ultrafine Chinese medicine particles, single-flavored Chinese medicine ultrafine pieces, and ultrafine Chinese medicine powders. Since the effective ingredients of plant medicine and animal medicine are mainly distributed in the cell and intercellular substance, and mainly in the cell, some people refer to the pulverization for the purpose of breaking the cells of Chinese medicinal materials as the "cell-level micro pulverization" of Chinese medicine. The traditional Chinese medicine powder obtained by the micro-grinding method is called "cell-grade Chinese medicine powder". Similarly, the traditional Chinese medicine prepared on the basis of cell-grade Chinese medicine powder is called "cell-grade Chinese medicine", or "micro-powder Chinese medicine" for short.
Some people call powders with a particle size greater than 1μm as "fine powder", and fine powders with a particle size less than 1μm as "ultrafine powder". In fact, in terms of the particle size of traditional Chinese medicines, micro and nano traditional Chinese medicines that are currently in the ascendant of research are also classified as ultra-micro preparations of traditional Chinese medicines. Lu Fuer et al. believe that "micron Chinese medicine preparations" belong to cell-grade micropowder preparations, which are a new dosage form developed by using modern high-tech and traditional processing and preparation techniques. Generally, the particle size should be 1-75μm. Traditional Chinese medicines within the scope can maintain the inherent pharmacodynamic material basis of traditional Chinese medicines. "Micron Chinese medicine" includes micron Chinese medicinal materials, micron extracts of Chinese medicines, and micron Chinese medicine preparations, which increase the cell wall breakage rate of Chinese medicinal materials by more than 90%. The so-called "nano Chinese medicine" refers to the effective ingredients, effective parts, original medicines, and compound preparations of traditional Chinese medicines with a particle size of less than 100nm manufactured by the application of nanotechnology. It is a kind of Chinese medicine powder after nanometerization. According to the above point of view, some researchers divide the ultrafine powder into micron level (>1μm), submicron level (0.1-1μm) and nano level (1-100nm), and divide the ultrafine powder technology into micron technology. , Submicron technology and nanotechnology.
Judging from the current research progress, although there are many names of Chinese medicine ultrafine grinders, related concepts and connotations are not the same, most of them think that the ultrafine grinding of Chinese medicine refers to the cell-level pulverization of Chinese medicine. The particle size is below 75μm. With the continuous deepening of research work, the definition or concept of ultrafine grinding of traditional Chinese medicine will be more scientific and accurate.
The Chinese medicine ultrafine grinder has a high cell wall breaking rate, which is conducive to the release and absorption of drugs. Ordinary crushed medicinal powder has a low rate of cell wall breaking. When the medicine enters the body, the powder particles of the medicinal powder absorb water and expand, and the active ingredients are continuously released from the cell wall and cell membrane through diffusion. Diffusion requires a concentration difference between the inside and outside of the cell. When the concentration difference between the inside and outside of the cell is small or balanced, the release rate of the active ingredient will be very slow or even stop. The active ingredient located in the inner cell is sometimes excreted before it can be released, so it is often not reached. To an effective therapeutic concentration.
After the Chinese medicine ultrafine grinder, the cell wall breakage rate is high, and the active ingredients are exposed before entering the body. After entering the body, the soluble ingredients are quickly dissolved. Great adhesion and tightly adhere to the mucosa of the inner wall of the gastrointestinal tract, so that the residence time in the gastrointestinal tract is prolonged, the absorption is more sufficient, and the absorption amount will increase. Since most of the cell wall is destroyed during crushing, the effective ingredients do not need to pass through the cell wall and cell membrane release process. In this way, ultrafine pulverization is far superior to ordinary pulverization in terms of drug release speed and release amount. Mineral medicine can reach micrometers even after ultra-fine grinding, which is conducive to the absorption of medicine and the improvement of curative effect.
Application analysis of calcium carbonate in industrial fillers
In recent years, calcium carbonate has been widely used in the plastic filling industry because of its excellent properties and low price. Compared with other inorganic mineral powder materials, the color of calcium carbonate itself is whiter, with better stability and better plasticization.
1. Rubber industry
Calcium carbonate is one of the largest fillers used in the rubber industry. A large amount of calcium carbonate is filled in the rubber, which can increase the volume of its products and save expensive natural rubber, thereby greatly reducing the cost. Calcium carbonate is filled into rubber to obtain higher tensile strength, tear strength and abrasion resistance than pure rubber vulcanizates.
2. Calcium carbonate in the binder and sealant
Calcium carbonate is widely used as a filler in adhesives and sealants. It has the advantages of narrow particle size distribution, large specific surface area, low oil and water absorption, etc. It can improve its rheological properties in PVC plastisols, enhance and reduce costs in silicone structural sealants, and can play an incremental reinforcement and heat-resistant role in hot melt adhesives. The adhesive can play a role in thickening and thickening. Application in adhesives and sealants can significantly reduce costs and improve bonding performance.
3. Paper industry
The use of calcium carbonate in the paper industry can ensure the strength and whiteness of the paper, and the cost is low. It can make the paper have good brightness, solid structure, easy writing, uniform coating, low friction, easy to dehumidify and easy to dry.
4. Plastic industry
Calcium carbonate can play a role as a skeleton in plastic products, which has a great effect on the dimensional stability of plastic products, and can also increase the hardness of the products, and improve the surface gloss and surface smoothness of the products. As the whiteness of calcium carbonate is above 90%, it also replaces expensive white pigments.
5. Paint industry
The amount of calcium carbonate in the paint industry is also relatively large, for example, the amount of calcium carbonate in thick paint is more than 30%.
6. Water-based coating industry
Calcium carbonate has a wider range of uses in the water-based paint industry, which can make the paint non-sediment, easy to disperse, and have good gloss. The amount of water-based paint is 20-60%.
7. Chemical building materials
In recent years, a new type of composite material-calcium plastic material has appeared in the building materials industry. This material has many excellent properties of wood, plastic and paper. It has the characteristics of heat resistance, chemical resistance, cold resistance, sound insulation, shock resistance, and easy processing. In packaging, building materials, pipes, etc., it largely replaces paper and wood.
8. Application of calcium carbonate in medicine, food, feed, etc.
Calcium carbonate is one of the important components in the pharmaceutical industry's culture medium. In addition to providing Ca elements, calcium carbonate also acts as a buffer for pH changes during stable fermentation culture. Therefore, calcium carbonate becomes a buffer for microbial fermentation in the pharmaceutical industry. Among pharmaceutical reagents, calcium carbonate can generally be used as a filler, while in anti-acid tablets, it has a certain medicinal effect. Calcium carbonate can be used as a food additive, and a small amount should be added to food, usually not more than 2%, to ensure the intake of calcium necessary for the human body. Because under normal circumstances, the total amount of calcium in the human body is about 1200 grams, 99% of which are present in the bones and teeth, and 1% is an essential component in the human blood, so carbonic acid is used in various food additives. Calcium is also one of them.
Article source: China Powder Network
Detailed description of jet mill
The jet mill is a device that uses high-speed airflow to achieve ultra-fine grinding of dry materials. It has a high full utilization rate of jet energy and has significant performance advantages such as no heating, no pollution, low wear and high precision. It is widely used in ultra-fine crushing of low-temperature, high-purity and high-hardness materials. For materials that are flammable, explosive, and easy to oxidize, inert gas can be used as a medium to achieve closed-circuit crushing, and the inert gas can be recycled.
The jet mill is composed of a jet mill, cyclone collector, dust collector, induced draft fan, electric control cabinet and other parts of a complete set of crushing system. After the compressed air is filtered and dried, it is sprayed into the pulverizing cavity at a high speed through the Laval nozzle. At the intersection of multiple high-pressure airflows, the materials are repeatedly collided, rubbed, and sheared to be pulverized. The pulverized materials enter the grading cavity with the ascending airflow. Under the action of the centrifugal force generated by the high-speed classification impeller and the centripetal force generated by the airflow, the coarse and fine particles are separated. The fine particles meeting the particle size requirements enter the cyclone collector and the dust collector through the gap of the classification impeller blades, and the coarse particles are thrown out by the classification impeller. Descend to the crushing area to continue crushing.
Currently widely used jet mills include flat jet mills, fluidized bed jet mills, and circulating tube jet mills.
The flat jet mill is used as a high-pressure airflow of smashing kinetic energy to enter the pressure-stabilized air storage bag outside the pulverizing cavity as an air distribution station. The airflow is accelerated into a supersonic airflow through the Laval nozzle and then enters the pulverizing mill cavity. Because the Laval nozzle and the crushing cavity are installed at an acute angle, the high-speed jet stream carries the animal material in the crushing cavity to make a cyclic movement, and the particles and the wall of the fixed target plate collide, collide and rub against each other to crush. The fine particles are guided by the centripetal airflow into the center outlet pipe of the crusher and enter the cyclone separator for collection. The coarse powder is thrown to the peripheral wall of the crushing chamber under the action of centrifugal force to make a circular motion and continue to be crushed.
The fluidized-bed jet mill is a process where compressed air is accelerated by Laval nozzles into supersonic airflow, and then injected into the crushing zone to make the material fluidized (the airflow expands into a fluidized bed suspension and boiling and collides with each other), so each particle Have the same state of motion. In the crushing zone, the accelerated particles collide and crush at the intersection of the nozzles. The crushed materials are transported to the grading area by the ascending airflow, and the fine powder that meets the particle size requirements is screened out by the grading wheel, and the coarse powder that does not meet the particle size requirements is returned to the pulverizing area to continue pulverization. The qualified fine powder enters the high-efficiency cyclone separator along with the air flow to be collected, and the dust-containing gas is filtered and purified by the dust collector and discharged into the atmosphere.
The raw materials of the circulating tube jet mill are fed into the crushing chamber by nozzles, and the high-pressure air flow is sprayed into the racetrack-shaped circulating tube crushing chamber with unequal diameter and variable curvature through a set of nozzles, accelerating the particles to collide, collide and rub each other to crush. At the same time, the swirling flow also drives the crushed particles upwards into the classification zone along the pipeline, and the dense material flow is divided under the action of the centrifugal force field in the classification zone, and the fine particles are discharged after being classified by the louver-type inertial classifier in the inner layer. The coarse particles return along the descending pipe in the outer layer and continue to circulate and crush.
Jet mills are widely used in industries such as chemical industry, minerals, metallurgy, abrasives, ceramics, refractory materials, medicine, pesticides, food, health products, new materials and so on. This is inseparable from its remarkable performance advantages. The performance characteristics of the jet mill are as follows:
1. Variable combination structure: one machine for two purposes, which can be crushed or graded separately;
2. Multi-stage cascade: It can be connected with 1-5 classifiers to produce products with narrow particle size distribution;
3. Wide range of crushing particle size: The particle size of the finished product can be adjusted between D97=3-150 microns, and the particle shape is good;
4. The whole system is sealed and crushed, with less dust, low noise, and the production process is clean and environmentally friendly;
5. The program control system is adopted, and the operation is simple.
Application and market of graphite electrodes
Graphite electrodes are mainly made of petroleum coke and needle coke as raw materials, coal tar pitch is used as a binder, and are made by calcining, batching, kneading, pressing, roasting, graphitization, and machining. It releases electric energy in the form of electric arc in an electric arc furnace. Conductor for thermal melting of the charge.
Classification of graphite electrodes
According to its quality index, it can be divided into ordinary power, high power and super high power. Graphite electrodes mainly include four types of ordinary power graphite electrodes, anti-oxidation coating graphite electrodes, high-power graphite electrodes and ultra-high-power graphite electrodes.
- Ordinary power graphite electrode
Graphite electrodes with current density lower than 17A/cm2 are allowed, which are mainly used for ordinary power electric furnaces for steelmaking, silicon making, and yellow phosphorus making.
- Anti-oxidation coating graphite electrode
A graphite electrode coated with an anti-oxidation protective layer (graphite electrode antioxidant) forms a protective layer that is both conductive and resistant to high-temperature oxidation, reducing electrode consumption (19%-50%) during steelmaking, and prolonging the use of electrodes Life span (22%~60%), reduce the power consumption of the electrode.
- High power graphite electrode
Graphite electrodes with a current density of 18-25A/cm2 are allowed, which are mainly used in high-power electric arc furnaces for steelmaking.
- Ultra-high power graphite electrode
Graphite electrodes with a current density greater than 25A/cm2 are allowed, and they are mainly used for ultra-high power steelmaking electric arc furnaces.
Characteristics of graphite electrodes
Advantages: good electrical conductivity, chemical stability, low electrode consumption, fast processing speed, good mechanical processing performance, high processing accuracy, small thermal deformation, light weight, easy surface treatment, high temperature resistance, high processing temperature, electrode bonding .
Disadvantages: The production cycle is long (the normal production cycle of graphite electrodes is generally about 90 days, and the production of electrode joints is four more processes than electrodes) and high cost.
There are five main elements to measure the performance of electrodes, which are processing speed, wear resistance, processed surface finish, processability and material cost. Copper electrodes are suitable for processing small and medium-sized workpieces with high surface roughness requirements; while graphite is suitable for processing various workpieces with low area roughness requirements, high electrode processing accuracy, high material unit prices, and high processing speeds.
Application of graphite electrode
- Application in die casting mold
In actual application, the processing time of graphite electrode is 1/2 of that of copper electrode with high precision, and the processing speed is 1.5 times that of copper electrode. According to statistics, if graphite electrodes are used for mold processing, small molds can save 15,000 yuan per set, medium-sized molds can save 50,000 yuan per set, and large-scale molds can save 85,000 yuan per set.
- Application in EDM
In the EDM process, tool click is the key determinant of the machining effect. Electrodes of different materials have a greater impact on processing efficiency, electrode loss, and surface quality. The high-performance graphite electrode has the unique advantages of small deformation, good thermal stability, high discharge efficiency, low loss, good conductivity, low density, no pollution to the environment, and reproducibility. It is an ideal electrode material. In Europe, more than 90% of the electrode materials used in EDM are graphite.
Graphite electrode market
According to the working current density, graphite electrodes are divided into ordinary graphite electrodes (RP), high-power graphite electrodes (HP), and ultra-high-power graphite electrodes (UHP). The main production and export countries of graphite electrodes abroad are the United States, Germany and Japan.
Graphite electrode raw materials include petroleum coke, coal pitch, calcined coke, needle coke and other major raw materials. The price of needle coke, the main raw material for graphite electrodes, rose the most, with a peak of 67% in one day. Needle coke accounts for 70% of the total cost of graphite electrodes, and ultra-high power graphite electrodes need to consume 1.05t needle coke. Needle coke can also be used in lithium batteries, nuclear power, aerospace and other fields.
Article source: China Powder Network
Important features of jet mill
The jet mill is the compressed air accelerated by the Laval nozzle into a supersonic airflow and then injected into the crushing zone to make the material fluidized (the airflow expands into a fluidized bed suspension and boiling and collides with each other), so each particle has the same state of motion .
As an important equipment for ultra-fine grinding, the jet mill has been widely used in chemical, pharmaceutical, battery materials, metallurgy, talc, quartz, graphite, abrasives, flame retardant materials, ceramics, pigments, food additives, pigments and other dry powder materials. Ultra-pure ultra-fine crushing.
Features of jet mill
In addition to fine particle size, jet mill products also have the characteristics of narrow particle size distribution, smooth particle surface, regular particle shape, high purity, high activity, and good dispersibility.
Since the compressed gas is adiabatic during the crushing process, the expansion produces a Joule-Thomson cooling effect, so it is also suitable for ultrafine crushing of low-melting, heat-sensitive materials.
Working principle of jet mill
The dry and oil-free compressed air or superheated steam is sprayed at high speed through the nozzle, and the high-speed jet moves the animal material at a high speed, causing the material to collide, rub and crush. The pulverized materials arrive at the classification area with the airflow, and the materials that meet the fineness requirements are collected by the collector. The materials that do not meet the requirements are returned to the crushing chamber to continue crushing until they reach the required fineness and are collected.
Due to the high velocity gradient near the nozzle, most of the pulverization occurs near the nozzle. In the crushing chamber, the frequency of particle-to-particle collisions is much higher than that of particle-to-wall collisions. Therefore, the main crushing effect in jet mills is the impact or friction between particles.
Application of Inorganic Filler in Coating Industry and Market Status
As an important material, coatings are widely used in construction and industrial fields. According to the application field, it can be divided into architectural coatings, industrial coatings, general coatings and auxiliary materials.
Architectural coatings: wall coatings, waterproof coatings, floor coatings, functional architectural coatings, etc.;
Industrial coatings: automotive coatings, wood coatings, light industrial coatings, marine coatings, anti-corrosion coatings, etc.;
General and auxiliary materials: blending paint, varnish, enamel, primer, putty, auxiliary materials (thinner, moisture-proof agent, drier, curing agent, etc.).
As the most used powder material in coatings, pigment fillers play an important role in improving, enhancing, and innovating the performance of coatings (coating films). Pigments for coatings include carbon black, iron oxide, titanium dioxide, etc., and fillers are also called inert pigments, volume pigments, and brighteners, which refer to white and colorless pigments that do not have tinting power and hiding power. According to different mineralogical characteristics and basic chemical composition, fillers can be roughly divided into carbonate, silicate, silica, barium sulfate and aluminum hydroxide.
- The role of inorganic fillers in coatings
Cost reduction: The thickness of the coating film can be increased by filling, which acts as a skeleton in the coating, making the coating film plump and thick, and therefore can reduce the cost of coating production.
Incremental enhancement: The filler can adjust the rheological properties of the coating, such as thickening, anti-settling, etc., and can also improve the mechanical strength of the coating film, such as improving abrasion resistance and durability.
Improve performance: The chemical composition, light, heat, electricity, magnetism and other properties of inorganic fillers can give coatings some functions.
- Selection index of inorganic filler
There are many types and specifications of fillers, and the use of high-quality and stable products is very important to ensure the performance of the coating. In the selection of fillers, in addition to paying attention to its chemical composition and mineral form, the filler's particle size and distribution, hardness, oil absorption value, aspect ratio and other characteristics are also indicators that must be considered.
Application of Inorganic Filler in Coating Industry
- Calcium carbonate
Basic performance: the most versatile extender pigment; chemically active, reducing film blistering, anti-mildew, and flame retardant; it not only reduces the cost but also acts as a skeleton, can increase the thickness of the film, improve the mechanical strength, abrasion resistance, and suspension.
High-quality natural calcium carbonate products are made of calcite, with high whiteness, and can be made into powders of various meshes required for coatings. Synthetic calcium carbonate is also called light calcium carbonate or precipitated calcium carbonate. Because the particles are finer, the oil absorption is greatly increased, and it is slightly alkaline. Synthetic calcium carbonate should not be used with pigments with poor alkali resistance. It can be used as a filler for water-based interior wall coatings in architectural coatings, but due to weather resistance and color retention It has poor performance and is rarely used in exterior wall coatings.
- Dolomite
Basic performance: The theoretical composition is w(CaO)=30.4%, w(MgO)=21.7%, w(CO2)=47.9%, often containing impurities such as Fe, Si and Mn. It has the characteristics of surface adsorption, can provide magnesium and calcium source, high refractoriness, large specific surface area, good heat insulation and heat preservation effect.
Dolomite powder can be used as a pigment filler in the coating industry to improve the weather resistance, rarity and scrub resistance of coatings. Mainly used in industrial protective coatings and marine coatings.
- Kaolin
Basic performance: The chemical composition is hydrated aluminum silicate, which has the properties of white color, low cost, good fluidity and suspension, chemical inertness, strong covering power, etc.; outstanding light resistance, acid, alkali and salt resistance, and good anti-settling effect.
Kaolin can increase the hiding power of titanium dioxide or other white pigments, and improve the rheology and gloss of coatings. In the paint, it mainly plays the role of filler and pigment substitute, and can reduce the demand for anggu dyes. Kaolin can also increase the hardness of the coating film, improve the quality of the coating film, and make the coating have good anti-corrosion, opacity and anti-settling properties. It can be widely used in water-based or solvent-based flat paint, semi-gloss paint, eggshell paint and special paint.
- Barium sulfate
Basic performance: There are usually two existing forms, namely natural barite powder and precipitated barium sulfate. Barium sulfate is an inert substance with high chemical stability, increased density, acid and alkali resistance, light resistance and heat resistance.
Barite powder is mainly used in primers in the coating industry. With its low oil absorption and low paint consumption, it can be made into thick film primers. And it has good filling, leveling and permeability resistance, which can increase the hardness and abrasion resistance of the coating film. Generally speaking, the performance of precipitated barium sulfate is better than that of natural products. It has high whiteness, fine texture and anti-blooming. The disadvantage is that it is dense and easy to precipitate.
- Wollastonite
Basic performance: The chemical composition is calcium metasilicate, and its length is 13 to 15 times the diameter. It has the characteristics of enhanced filling, chemical stability, good thermal stability and dimensional stability, excellent electrical properties, and high whiteness and brightness.
Wollastonite can increase the bright tone of white paint, and can replace white powder and titanium dioxide without reducing the whiteness and hiding power of the paint. Wollastonite can also improve the leveling of coatings and can also be used as a good suspending agent for coatings. Wollastonite used in primers can provide anti-corrosion performance, and can improve scratch resistance and crack resistance.
- Mica powder
Basic performance: Mica powder exists in nature in the form of multi-layer crystalline flakes. It has good transparency and high refractive index, high insulation strength and large electrical resistance, and excellent corona resistance and Mechanical properties and acid and alkali resistance.
Mica powder can impart flexibility, water resistance, weather resistance, chemical resistance, heat resistance and electrical insulation to the coating film. The horizontal arrangement in the paint can prevent ultraviolet radiation and protect the coating film, and can also prevent moisture from penetrating. In architectural coatings, the introduction of mica powder can improve the crack resistance of the coating film and improve the scrubbing resistance. A small amount of mica is used as a special component of steel structure primer, which can improve salt spray resistance and durability.
- Talcum powder
Basic performance: Talc powder is a magnesium silicate mineral. The layered basic unit structure is stacked on each other through extremely weak van der Waals force, and the layers are easily separated, giving it a certain degree of softness. It has good electrical insulation, heat resistance, chemical stability, lubricity, oil absorption, hiding power and mechanical processing properties.
In the field of industrial coatings, especially in primers, the introduction of talc powder can improve the corrosion resistance and crack resistance of the coating film, and can improve the adhesion and sanding properties, and can also play a role in preventing settling and sagging.
- Feldspar powder
It is a typical frame-like structure of mineral filler. According to different cations, feldspar powder mainly exists in three forms of albite, potash feldspar and anorthite. The morphology of feldspar powder is composed of nodular particles with edges and corners. Compared with spherical or ordinary block fillers, it can form a denser coating film, impart high wear resistance and scratch resistance to the coating film, and improve the coating film performance. Anti-corrosion performance.
- Silica
It can be divided into two categories: natural and artificial.
Natural products include crystalline silica, that is, quartz sand, which is mainly used in the preparation of architectural real stone paint.
There is also amorphous natural silicon dioxide, namely diatomaceous earth. Due to its low density and porosity, it is commonly used in interior wall coatings to absorb and eliminate odors. In addition, diatomaceous earth has an ionic effect, which can decompose water molecules into positive and negative ions, thereby generating strong oxidation and having a certain sterilization effect.
Artificial products include precipitated silica and synthetic fumed silica.
Precipitated silica uniformly dispersed in the coating film can produce a micro-rough surface, which makes the light diffusely reflected and has a strong matting effect.
Synthetic fumed silica, also known as white carbon black, has a thickening effect and exhibits certain thixotropy in coatings. In the water-based acrylic system, the introduction of silica may reduce the aging resistance of the coating film. This is because the metal ion impurities contained in silica will cause the coating film to undergo photo-oxidative degradation under ultraviolet light irradiation, and the silanol groups in the silica channels will also promote the photodegradation reaction.
- Bentonite
Basic properties: The special layered structure gives bentonite special properties, such as water absorption, swelling, thixotropy, rheology, etc.
Bentonite is mainly used as an auxiliary agent in coatings, such as thickeners, anti-settling agents, dispersants, etc., to prevent the sedimentation of pigments and fillers in the coatings.
According to the type of bentonite, calcium-based bentonite and sodium-based bentonite are mainly used in water-based coatings, while organic bentonite is mainly used in solvent-based coatings, and lithium-based bentonite can be used in water-based coatings.
- Aluminum hydroxide
As a flame-retardant filler, aluminum hydroxide has good thermal stability and has the three major functions of flame-retardant, smoke suppression and filling. It is the most important inorganic filler in fire-retardant coatings. The flame-retardant principle is that aluminum hydroxide releases water at high temperatures, an endothermic reaction occurs, and the water evaporates and consumes additional energy. After the aluminum hydroxide is decomposed, a barrier layer is formed, which can slow down the flow of oxygen and the rate of generation of other gases. The resulting aluminum oxide residue is deposited on the surface to isolate the oxygen and achieve the effect of inhibiting combustion. In addition, aluminum hydroxide's low absorption of ultraviolet light makes it very suitable for UV curing coating systems.
Market overview of the coating industry
The increase in demand in the coatings market is mainly due to the growth of investment in the construction industry, the development of the automobile industry, the increase in urban population and the improvement of the global economy. According to data from the World Paint and Coatings Industry Association (WPCIA), with the exception of 2015, the global coatings market showed a growth trend from 2012 to 2019. In 2019, the global coatings market was worth 172.8 billion U.S. dollars, an increase of 4.8% compared to 2018.
Competition in the global coatings market is fierce. Due to the large number of coating categories and the large differences in downstream demand in the industry, there are a large number of companies and the industry is relatively fragmented. From a regional perspective, Asia Pacific, Europe and North America are the leading regions in the global coatings industry. The Asia-Pacific region is the world's largest coatings market. The Asia-Pacific region accounted for 57% of sales in 2019, an increase of 7pct compared to 2018.
Article source: China Powder Network
The development trend of superfine grinding equipment
Ultrafine pulverization technology is a new pulverization technology developed to meet the requirements of modern technology. It can process raw materials into micron or even nanometer-sized powder. It has been used in chemicals, food, pesticides, cosmetics, dyes, coatings, electronics, aviation It is widely used in many fields such as aerospace.
With the continuous increase of social demand, ultra-fine grinding equipment is facing great challenges in terms of performance, finished product quality, service life and other issues. Therefore, equipment manufacturers are increasing their own research and development efforts, and constantly improving equipment in the ultra-fine grinding The adjustment and control technology of crushing force, particle size distribution, grain shape and crystal shape at work, in order to achieve more efficient production.
This requires all machinery manufacturers to make targeted improvements to the environmental protection and low-consumption performance of ultra-fine powder processing and production equipment, and strive to achieve low energy consumption, high output, no pollution, and good particle size of finished materials in ultra-fine grinding technology. Unique performance advantages such as good dispersibility can improve the competitiveness and market share of ultra-fine grinding equipment.
Modern production not only pursues production efficiency and finished product quality, but also develops in the direction of environmental protection and energy saving. The same is true in the pharmaceutical machinery industry. Looking at the requirements of modern social productivity, the overall development trend of material ultrafine grinding technology is the reverse development of low cost, high efficiency, strong controllability, good dispersion, and stable quality. Various types of ultrafine grinding equipment put forward higher technical requirements.
Modern engineering technology will require more and more high-purity ultra-fine powder, and ultra-fine powder technology will play an increasingly important role in high-tech research and development. High-purity ultra-fine powder is prepared by chemical synthesis, but the cost is too high and it is extremely difficult to use in industrial production. The main method of obtaining ultra-fine powder is still mechanical pulverization. Ultra-fine pulverization technology is a synthesis of various technologies, and its development also depends on the progress of related technologies. Therefore, the main development trends of ultrafine grinding equipment are as follows:
(1) Develop fine grading equipment matched with ultra-fine grinding equipment.
(2) Develop ultra-fine grinding equipment with low energy consumption, small footprint and large processing capacity.
(3) Integrated development of equipment and process research. Superfine grinding and supporting equipment must adapt to specific material characteristics and product indicators, and scale models must adapt to a large range.
Principles and advantages of activated carbon ultrafine pulverizer
Activated carbon material has stable chemical properties, high mechanical strength, acid resistance, alkali resistance, heat resistance, insoluble in water and organic solvents, and can be recycled. It has been widely used in chemical engineering, environmental protection, food processing, metallurgy, drug refining, military chemical protection And so on in various fields. At present, modified activated carbon materials are widely used in sewage treatment, air pollution control and other fields, showing bright prospects in the treatment of environmental pollution. Activated carbon can exert its value to a greater extent after being superfinely pulverized.
Activated carbon has the characteristics of developed pore structure, large specific surface area and smooth surface, so ordinary powder crushing equipment is not suitable for crushing activated carbon. In view of the high production cost and low production efficiency of activated carbon, the ultra-fine pulverizer uses hammers, blades, rods, etc. on the high-speed rotating body to impact the crushed materials, and uses the fierce impact of the material and the rotating body to fly at high speed. The high-speed impact between the materials and the shearing and grinding of the rotating body and the stator or the side wall realize the purpose of ultra-fine crushing of the materials.
The unique crushing mechanism determines its wide range of applications, powerful functions and changeable characteristics: it can be applied to plant fiber materials, plant shell materials, and non-mineral light calcium, heavy calcium crushing, etc. . Compared with the traditional coarse crusher, its fineness can be crushed to finer: the finest can reach 1500 mesh (8 microns); the single processing capacity is larger: the current maximum processing capacity is 8 tons per hour at 1000 mesh.
After the reorganization of the main machine structure and the adjustment of the rear supporting components, this machine can be made into a high-efficiency dispersing machine. Its dispersing efficiency is high: a single unit has a large processing capacity; a high dispersing fineness: it has been applied to nano-active carbonic acid. Dispersion of calcium; wide range of applications: when the hardness of the material is moderate, it can be used to disperse the material under conditions such as compaction after drying, agglomeration after long-term storage, and long-term dampness. During the break up operation, this machine also has the advantages of maintaining the original crystal grain shape and protecting the surface film of the powder.
The complete set of equipment comes standard with an impact mill host, a vertical high-precision turbine classifier, a cyclone collector, an electronic pulse bag dust collector, and supporting motors and electronic control components.