Service
We customized and provided high cost-performance ratio products to more than 3000 customers in more than 100 countries and regions around the world , meanwhile, we also provide them with detailed one-stop, professional and expert-level services, relieving our customers’worries.
Inspection & delivery
Strict production process control, packaging and boxing suitable for land and sea transportation
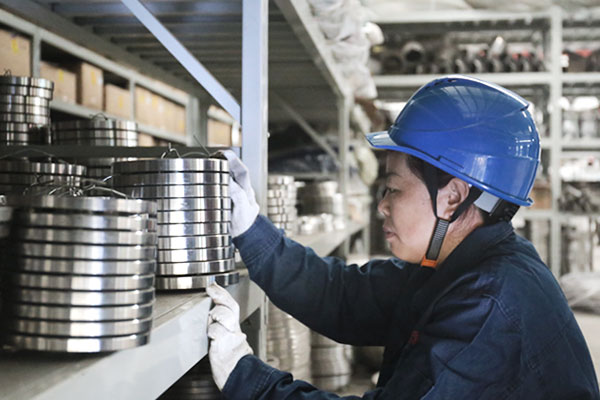
Stock order verification
The merchandiser verifies the model, quantity and accessories of the equipment ordered by the customer in detail in accordance with the sales contract to ensure that the stocking is fully matched with the order.
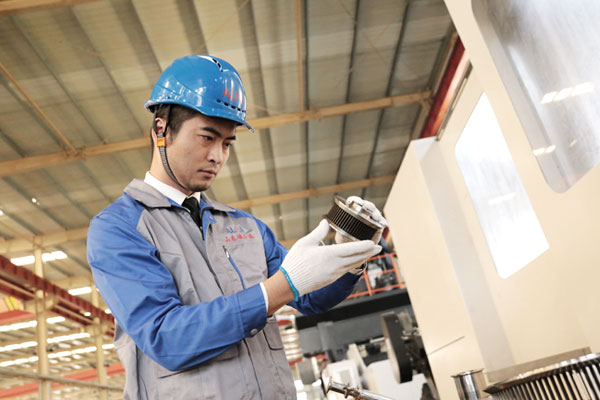
Equipment quality inspection
After the production system completes the equipment production, the quality inspector strictly inspects the records item by item according to the quality inspection details to ensure the quality of each equipment to be installed.
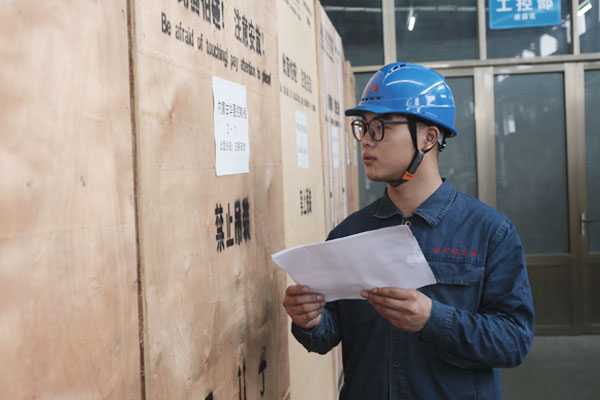
Packing List Review
Before the equipment is packed and shipped, the merchandiser will check the packing list one by one to avoid missing or under-delivery.
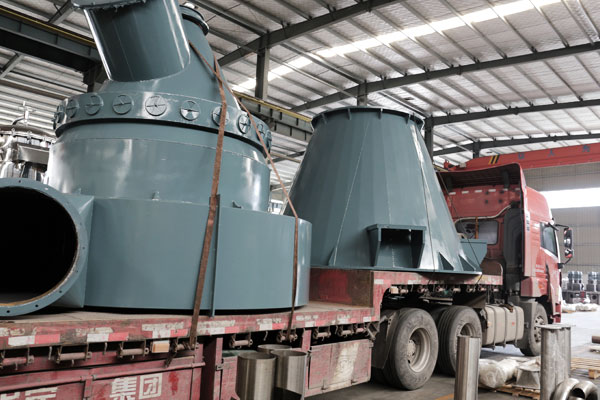
Scientific Packaging & Transportation
In equipment boxing and packaging, we adopt professional packaging and modular solutions to ensure the safe and non-destructive delivery of equipment.
Installation, Commissioning & Training
We believe that to make any equipment run successfully and reliably, it must start with a careful and thorough arrangement, well-executed installation, commissioning and trial production. After you purchase ALPA equipment, our after-sales service team is ready to provide services for you at any time.
Our services include the following:
- Installation & assembly
- Empty machine debugging
- Debugging with materials
- Site acceptance test (SAT)
- On-site training
- Remote Technical Support
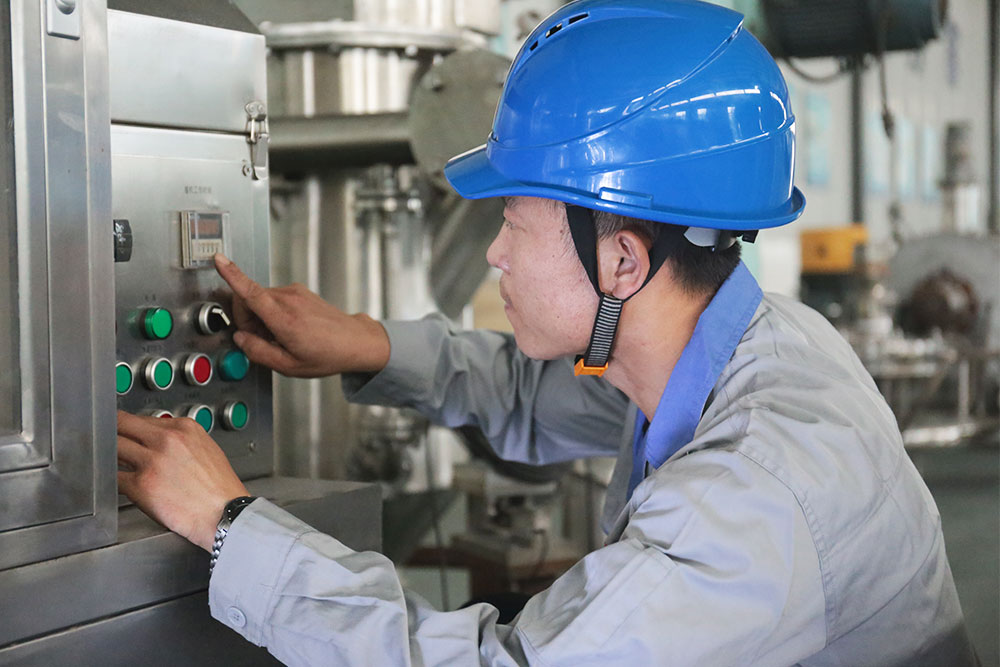
Original Accessories
ALPA provides original accessories for all equipment and systems
Any mechanical parts, after a period of use, will be worn or damaged. Therefore, your machine may need to be replaced with new parts. If you are using ALPA machines, don’t worry at all. We have made sufficient preparations to guide you to quickly complete the replacement of accessories in the shortest possible downtime, and debug to full marks.
1. Maintain the excellent performance of the machine, just like a new machine;
2. The price is reasonable and fair, and will not add higher costs;
3. The quality is reliable and the service life of the machine is improved.
The accessories are consumables. It is recommended that you stock a few more sets of wearable accessories when buying the machine. The price is cheaper and it saves more waiting time.
Process Upgrade & Optimization
Usually, after the system has been running for several years, it is recommended to use the process optimization service. With the production of new research results, the resulting process upgrades will bring new changes to your production. In order to apply the new process to your system in a timely manner, under your authorization, we can remotely access your system, evaluate your system performance, or visit your door to communicate with you to determine whether new parts replacement, control upgrades, process adjustments are needed Wait.
The continuous upgrading of the process is inseparable from technological innovation. Since 2005, ALPA has established cooperative relations with major universities, scientific research institutions, and advanced international group companies in the industry to strengthen the complementary resources of schools and enterprises, share technology in the industry, and enhance the company’s product innovation capabilities.
1-3 Months Lead Time
Under the premise of ensuring quality, the delivery time is 1-3 months.
High Cost Performance
The quality is consistent with German and Japanese brands, but the price is only 1/3.
Worry-free After-sales
Having trouble with the production process? Do not worry. We will be waiting for you 24 hours a day.
Installation & Training
Help you install and debug on site, and provide complete operation training.